Most of us own and use torque wrenches when we are working on our bikes, but not many of us "Do-It-Yourself-ers" will go to the bother and considerable expense of having our torque wrenches sent out for calibration. I don't know about the rest of you, but being a "type A" guy, I've always wondered just how inaccurate my old clicker wrenches are. How much should I trust them?
In a fit of age related insomnia last night, I came up with a plan for checking my torque wrenches to ensure that I won't under, or worse over torque any important fasteners. To begin with, neither of them are particularly expensive wrenches when new, and neither have any means of actually adjusting their calibration settings that I can see. So this is just a check, to know how far and which way they are off. If they are bad enough it might motivate one to replace a clearly defective torque wrench.
Here's what I came up with. I hooked up the torque wrench to an already highly torqued axle nut (90 ft-lbs on my WR250) and then hung barbell weights off of the handle. I could then iteratively adjust the wrench's torque to find the point where the clicker just barely clicks. Then do a little math and you can determine exactly how accurate the wrench is.
Here's a thousand words of the set-up:
In the above picture, due to the angle of the shot it looks like the wrench is not parallel to the leaf strewn floor. It actually is, and that is an important detail. It is also not obvious that the weights are hovering a few inches above the floor. Unfortunately, the case box is empty, so no beer for breakfast today. :angry:
You could use anything you want to hang the weights. I used a length of solid core electrical house wire and a broken screwdriver blade that I had laying around and made a little weight hanger from them:
You'll note that I used the white (neutral) wire. One wouldn't want to get shocked while doing this calibration check!
(NERDY electrical joke)
To determine how much torque the hung weight is applying you'll want to pre-weigh the barbell weight on a reasonably accurate scale to find its actual weight. I used my package shipping scale (good enough for UPS!) and found that my 2 weights marked as 25 lbs are actually 24.5 lbs each. Then you'll need to multiply that weight by the length of the torque wrench (in feet to get ft-lbs) from the center of the square drive to the point on the handle that you hung the weight from.
In the pictured example, I have two 24.5 lb weights (49 lbs total) hanging 17.5" from the drive end. 17.5 / 12 = 1.458 feet x 49 lbs = 71.46. So that tells me how much torque is actually being applied to the wrench. Somewhat miraculously, my torque wrench would just barely click over between 71 and 72 on the rotary handle. Sweet! :thumbsup:
I also ran the same experiment, but with a single barbell weight suspended, and the clicker went off at 36 1/2. The math said 1.458 x 24.5 = 35.73, so it appears at lower settings I will be slightly under torquing fasteners, but still within a reasonable degree of accuracy.
I then checked my small 3/8" drive torque wrench using a single 24.5 lb weight, but with the shorter handle I hung the weight only 8" from the drive. It clicked over at ~ 200 inch lbs. And the math says that I was applying 24.5 lbs x 8 inches = 196 inch lbs. :thumbsupsmileyanim:
I now can have good confidence that my old, cheap-*** torque wrenches are measuring my fastener torque settings with adequate accuracy, and should be able to sleep better at night.
How are your wrenches?
.
In a fit of age related insomnia last night, I came up with a plan for checking my torque wrenches to ensure that I won't under, or worse over torque any important fasteners. To begin with, neither of them are particularly expensive wrenches when new, and neither have any means of actually adjusting their calibration settings that I can see. So this is just a check, to know how far and which way they are off. If they are bad enough it might motivate one to replace a clearly defective torque wrench.
Here's what I came up with. I hooked up the torque wrench to an already highly torqued axle nut (90 ft-lbs on my WR250) and then hung barbell weights off of the handle. I could then iteratively adjust the wrench's torque to find the point where the clicker just barely clicks. Then do a little math and you can determine exactly how accurate the wrench is.
Here's a thousand words of the set-up:
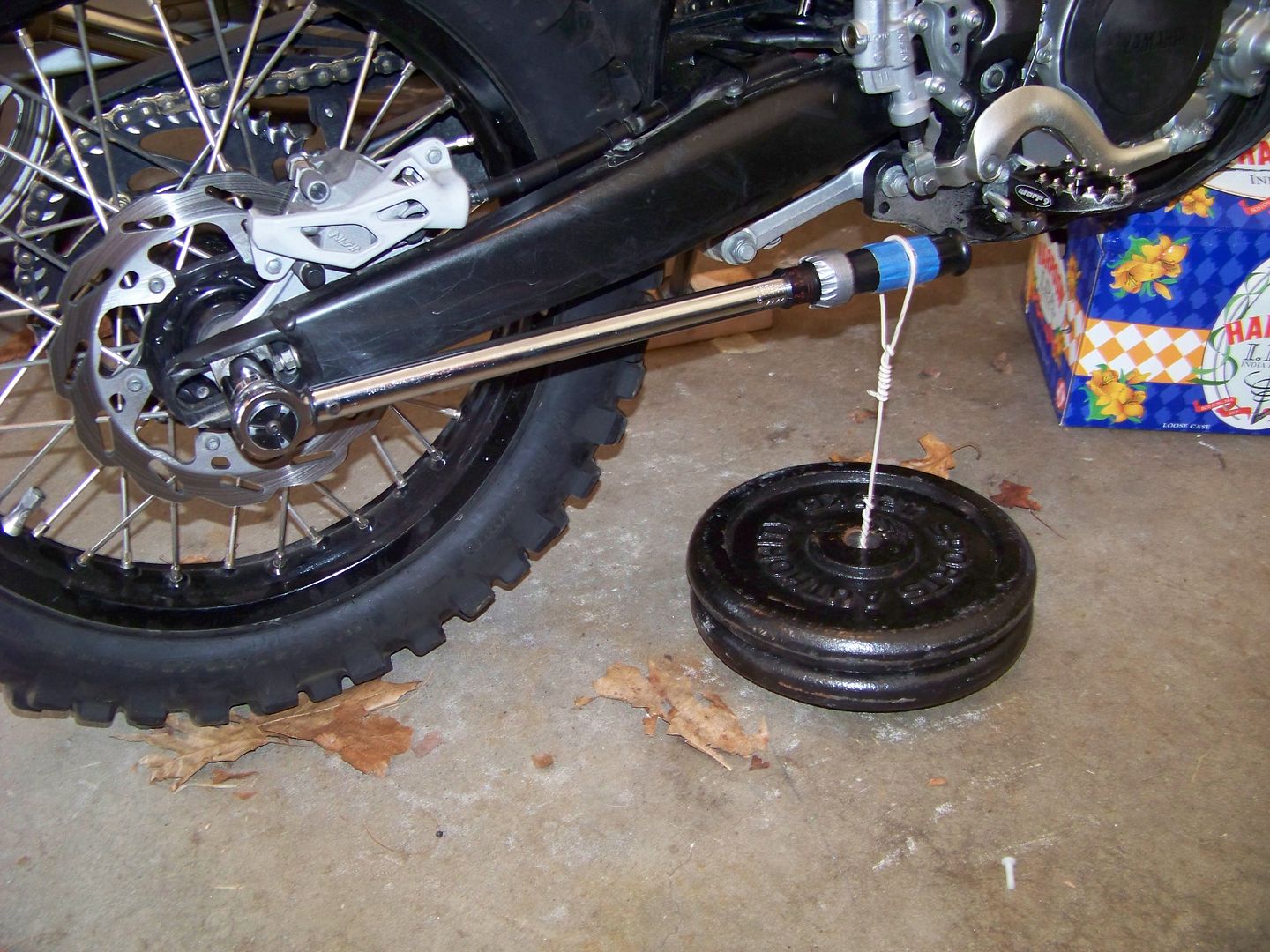
In the above picture, due to the angle of the shot it looks like the wrench is not parallel to the leaf strewn floor. It actually is, and that is an important detail. It is also not obvious that the weights are hovering a few inches above the floor. Unfortunately, the case box is empty, so no beer for breakfast today. :angry:
You could use anything you want to hang the weights. I used a length of solid core electrical house wire and a broken screwdriver blade that I had laying around and made a little weight hanger from them:
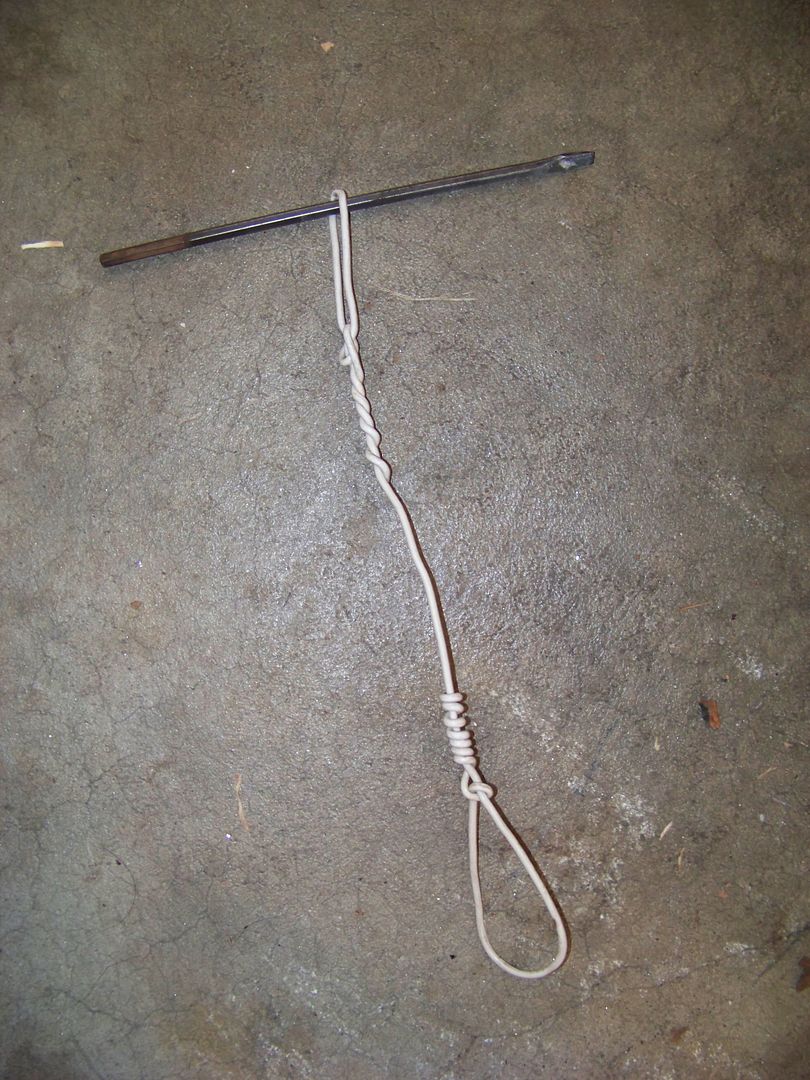
You'll note that I used the white (neutral) wire. One wouldn't want to get shocked while doing this calibration check!
(NERDY electrical joke)
To determine how much torque the hung weight is applying you'll want to pre-weigh the barbell weight on a reasonably accurate scale to find its actual weight. I used my package shipping scale (good enough for UPS!) and found that my 2 weights marked as 25 lbs are actually 24.5 lbs each. Then you'll need to multiply that weight by the length of the torque wrench (in feet to get ft-lbs) from the center of the square drive to the point on the handle that you hung the weight from.
In the pictured example, I have two 24.5 lb weights (49 lbs total) hanging 17.5" from the drive end. 17.5 / 12 = 1.458 feet x 49 lbs = 71.46. So that tells me how much torque is actually being applied to the wrench. Somewhat miraculously, my torque wrench would just barely click over between 71 and 72 on the rotary handle. Sweet! :thumbsup:
I also ran the same experiment, but with a single barbell weight suspended, and the clicker went off at 36 1/2. The math said 1.458 x 24.5 = 35.73, so it appears at lower settings I will be slightly under torquing fasteners, but still within a reasonable degree of accuracy.
I then checked my small 3/8" drive torque wrench using a single 24.5 lb weight, but with the shorter handle I hung the weight only 8" from the drive. It clicked over at ~ 200 inch lbs. And the math says that I was applying 24.5 lbs x 8 inches = 196 inch lbs. :thumbsupsmileyanim:
I now can have good confidence that my old, cheap-*** torque wrenches are measuring my fastener torque settings with adequate accuracy, and should be able to sleep better at night.
How are your wrenches?
.
Last edited by a moderator: