ionbeam
2 FUN
Judging from the number of failures of the Throttle Position Sensor I believe we can now rename it Total Piece of Shit.
These are the three primary parts to the TPS.
Attention to all you throttle spring releasers, the left side spring serves two functions. It is tightly wound to provide return spring tension for the throttle body shaft and ensures that the two pickup brushes (wipers) are firmly in contact with the resistors.
The center item is the actual body of the TPS. The black trails are resistive material screened onto the inert white backing. The far left terminal is Ground, the far right terminal is +5 volts from the ECU, the terminal just to the left of +5 is the signal terminal going back to the ECU. As the wipers slide along the resistor trails a varying voltage that is proportional to the throttle position gets returned to the ECU.
The right side object has the two pick up brushes, one riding on the +5 volt resistor and the other riding on the signal resistor. On my TPS the resistor that goes +5 volts to ground is 5.28k ohms and the resistor going to the signal terminal is <100 ohms.
These are the two wipers that ride along the resistive material. They are made up of individual wires. Note the wiper on the right side, at the very right edge, has one wire bent out. The wipers themselves have strong spring tension which is then supplemented by the large holding spring.
The arrows in the above picture show where the wipers sit at idle.
This is the source of the problem with the TPS. Normally, resistive material is carbon mixed with silica then fired to make a very hard glass like resistor. The TPS resistive material is made of a softer plastic type product. The wiper's individual wires actually have cut clear thorough the resistive material. When viewed under a microscope the base material is visible in the bottom of the grooves. Normally, this type of resistive material has its value determined based on it being a 'sheet', once cut the value will start to change. I measured a few of the furrows and they are just a bit wider than the wiper wires so there isn't sure contact side to side and the bottom is worn through. Additionally, and most importantly, the thinned material is no longer resistively stable under thermal changes. In particular, once it hits some critical temperature it goes from resistive to non-resistive. Said inversely, it goes from somewhat conductive to not conductive at all in those furrowed areas. This is one reason that a TPS can pass test at room temperature but fail once the engine heats up.
The arrows point out where the brushes have worn away the resistive material at idle and at roughly 25-30% throttle. For me that is around 3k RPM. You can also see that it has started to burn in the highly worn places.
The TPS I put in has a new P/N that is the same on the '06 so I take that to mean there has been some kind of a change to the part. It will take time or an autopsy of the '06 part to find out if it has been improved. I will note that my mostly solved surging is now back with the new TPS. I don't yet know if that is coincidence or related. My engine now runs with abrupt throttle response like the '06 people are reporting.
These are the three primary parts to the TPS.
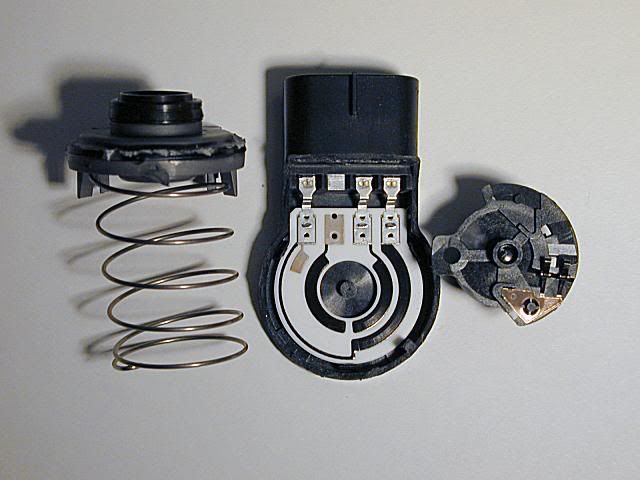
Attention to all you throttle spring releasers, the left side spring serves two functions. It is tightly wound to provide return spring tension for the throttle body shaft and ensures that the two pickup brushes (wipers) are firmly in contact with the resistors.
The center item is the actual body of the TPS. The black trails are resistive material screened onto the inert white backing. The far left terminal is Ground, the far right terminal is +5 volts from the ECU, the terminal just to the left of +5 is the signal terminal going back to the ECU. As the wipers slide along the resistor trails a varying voltage that is proportional to the throttle position gets returned to the ECU.
The right side object has the two pick up brushes, one riding on the +5 volt resistor and the other riding on the signal resistor. On my TPS the resistor that goes +5 volts to ground is 5.28k ohms and the resistor going to the signal terminal is <100 ohms.
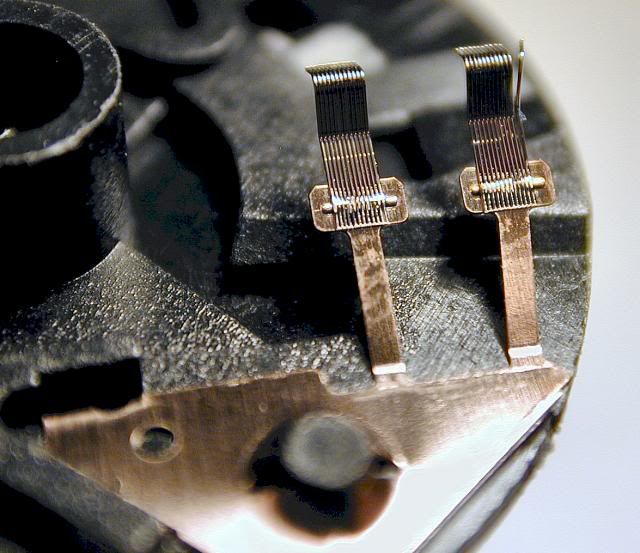
These are the two wipers that ride along the resistive material. They are made up of individual wires. Note the wiper on the right side, at the very right edge, has one wire bent out. The wipers themselves have strong spring tension which is then supplemented by the large holding spring.
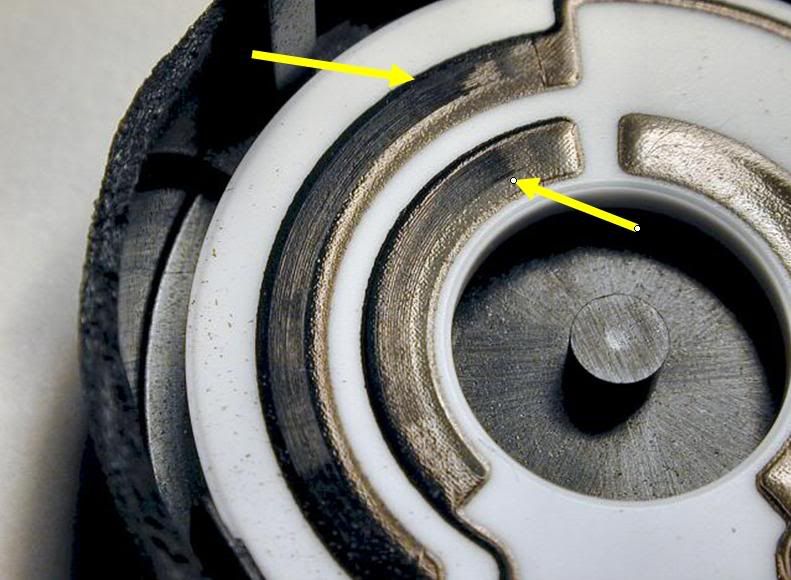
The arrows in the above picture show where the wipers sit at idle.
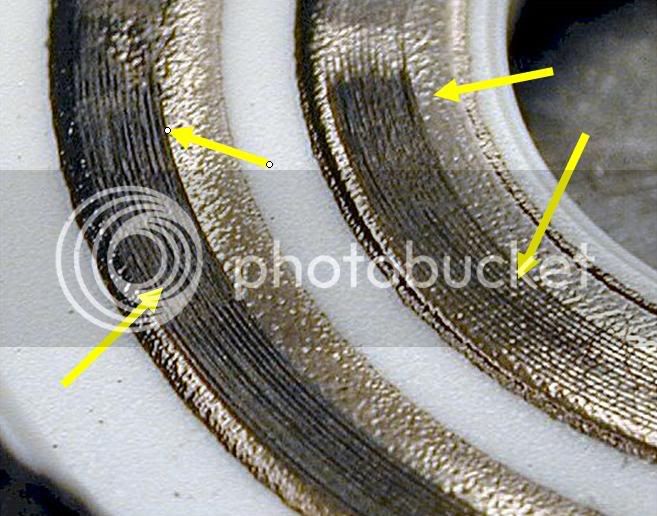
This is the source of the problem with the TPS. Normally, resistive material is carbon mixed with silica then fired to make a very hard glass like resistor. The TPS resistive material is made of a softer plastic type product. The wiper's individual wires actually have cut clear thorough the resistive material. When viewed under a microscope the base material is visible in the bottom of the grooves. Normally, this type of resistive material has its value determined based on it being a 'sheet', once cut the value will start to change. I measured a few of the furrows and they are just a bit wider than the wiper wires so there isn't sure contact side to side and the bottom is worn through. Additionally, and most importantly, the thinned material is no longer resistively stable under thermal changes. In particular, once it hits some critical temperature it goes from resistive to non-resistive. Said inversely, it goes from somewhat conductive to not conductive at all in those furrowed areas. This is one reason that a TPS can pass test at room temperature but fail once the engine heats up.
The arrows point out where the brushes have worn away the resistive material at idle and at roughly 25-30% throttle. For me that is around 3k RPM. You can also see that it has started to burn in the highly worn places.
The TPS I put in has a new P/N that is the same on the '06 so I take that to mean there has been some kind of a change to the part. It will take time or an autopsy of the '06 part to find out if it has been improved. I will note that my mostly solved surging is now back with the new TPS. I don't yet know if that is coincidence or related. My engine now runs with abrupt throttle response like the '06 people are reporting.

Last edited by a moderator: