I'm starting this post as a discussion point for the merits of gravity vs. pump for aux fuel tanks. The information I'm posting is based upon my VERY LIMITED experience - so If something's going on that I don't understand, I'll tell you. I'm not going to list anything that is 'hearsay.' In other words, if I haven't experienced it, I won't put it down.
I look forward to the members of this forum with decades of experience posting up !!
It doesn't matter what bike it was installed on. My FJR, your 1969 R bike, his Goldwing. We're trying to examine Gravity vs. Pump.
My intent is NOT to have a "Mine is bigger than yours" or "Manufacturer ABC is better than Manufacturer XYZ." What I'm looking for here is input from this forum of personal experiences - prats and pitfalls, your personal history with tanks, which method of fuel transfer do you prefer, etc., etc., etc.
Opinions are very welcome, but please try to back them up with facts and/or experiences.
First - a few basics that apply to either style of fuel transfer. If you know of additional facts, please post them. These are here because these physical traits affect fuel transfer.
1. Fuel Expands under heat. In some cases, dramatically so. The design has to be able to deal with the expansion of the fuel. This is done by a vent opening on the aux tank that allows expanding fuel to escape.
2. Expanding fuel builds pressure if not allowed to escape. This is NOT a desirable trait.
3. As the fuel is transferred from the aux to the main, the volume of fuel moving from the aux tank must be replaced with a similar volume of air from the atmosphere. This is accomplished by the same vent hole. See #1.
4. And while obvious, I'll put it here - there must be ROOM in the main tank for the transferring fuel to go - and the air in the main tank must be able to vent out as it is displaced by incoming fuel.
OK - Let's do a basic examination of gravity feed:
(This is kind of a 'brain dump' for me - I'm just kind of thinking via my keyboard)
Gravity pulls DOWN. Liquid will always flow to the lowest point, as it is pulled there by gravity.
Logic - a gravity transfer tank will need to be mounted in such a manner that the fuel exit (and level) of the aux tank is HIGHER than the fuel entrance (and level) of the main tank. This way, when then valve is opened, the fuel will flow from HIGH to LOW.
Flow rate equates to time. Faster flow rate = less time, slower flow rate = more time.
Logic - the larger the inner diameter of the fuel lines, the faster the flow rate. The greater the differential in elevation (we're talking inches here, folks !) the faster the flow rate. (Very minor difference, unless you were to mount the tank on some sort of superstructure 6 feet above your head :blink: )
Gravity is always present. (Unless I missed the event, I've never noticed it leaving.)
Logic - does not require mechanical assistance.
Flow DIRECTION is dependent upon gravity -
Logic - Fuel flows from high to low. (redundant, I know. but very important. )
And Pump feed:
Simple - a fuel pump is installed to transfer the fuel REGARDLESS of tank elevation differentials.
A fuel pump could be used on a tank that might otherwise function as a gravity feed tank.
Logic - using a fuel pump allows the placement of the aux tank to be agnostic in elevation to the main tank. (does that make sense?)
Fuel pumps require electricity - or a gerbil on a wheel, whichever you choose.
Logic - this is a failure point.
Fuel pumps produce pressure -
Logic - fuel lines and fittings must be able to accommodate the increased pressure.
Fuel pumps vary in flow rates (usually listed by pressure)
Logic - it is possible to install a pump with TOO MUCH PRESSURE and make a huge mess of your garage when the fire department puts out the resulting conflagration.
Some fuel pumps can burn out when operated dry.
Logic - research what you buy. This is not a component to save $$ on.
And now to fuel transfer differences - and this is from my personal experience.
Gravity feed - I have limited experience. I installed a gravity feed tank last November, which was quite a learning curve for me.
This tank was on my bike long enough to run three fills through it. If you notice, it's much higher than a pillion mounted tank - and the transfer rate was relatively quick, due to the large differential between fuel levels. (The bottom of the aux was higher than the top of the main) It was possible to open the petcock, and have this tank empty through the main tank overflow valve if I wasn't watching the main tank level. This meant I really had to pay attention, and make very sure that the valve was closed when I filled it. So - I found myself riding along, trying to remember if I'd closed the darn thing! The petcock was not easily accessable when riding - I had to stop the bike, then twist backwards, and open the valve. I simply could not do it while underway. This could be dealt with by a different fuel line routing, perhaps an in-line valve for the transfer. The fuel movement inside the tank was very noticible - sitting up high like that, any wave motion was amplified. I overcame this by installing anti-slosh foam in the tank as per IBA regs. Should I elect to use it again, I will also have to engineer a proper static ground for it.
I have no personal experience with a "pillion mount" style of tank. Many of my fellow riders do, and I look forward to hearing of their experiences.
Pump feed -
I installed a "underhung" design, as I had discussed with Ron Sampson his need to adapt the long standing Ron Major design to the FJR1300. He used my bike as the mule for this - and I worked with him extensively to get the system 'tweaked.'
IMHO -in retrospect - I should have gone with a pump to begin with. I could still rig a pump on my gravity feed tank, and not have to deal with the valve position.
Using the pump feed I find to be substantially easier. I can simply turn on the pump via a LED (visual indication) rocker switch on my cowling, and inside of 25 minutes, 4.3 gallons of fuel transfers to the main tank. I think the ability to pump the fuel easily with a minimum of fuss is of benefit. This transfer time could be improved upon, as I used 1/4" line and fittings. This is due to the tight radii that I needed to obtain with the line routing. The 5/16" line simply would not make the turns without collapsing.
The installation of a fuel pump is more complex - wiring, fusing, additional fuel lines, etc., but it's certainly not above a reasonably competent wrench. If you've got the self confidence to do the main tank penetration, the rest of the installation should be easy. If you could install a gravity tank, you could install a pump.
The downside? COST. As there are more components, the cost to install a pump is greater than gravity feed.
I did the final install last May - and have now put just over 7K miles on it. It has functioned as designed without any problems. I continually check the nuts and bolts, I check for abrasion on the fuel lines, leaks on the Herbie clamps, etc. But so far - it's been bulletproof. Time will tell.
So - that's where I'm at - I have heard many additional comments and stories from forum members - but not having matching experiences, I can't relate those to you.
Pump vs. Gravity? Well ?
I look forward to the members of this forum with decades of experience posting up !!
It doesn't matter what bike it was installed on. My FJR, your 1969 R bike, his Goldwing. We're trying to examine Gravity vs. Pump.
My intent is NOT to have a "Mine is bigger than yours" or "Manufacturer ABC is better than Manufacturer XYZ." What I'm looking for here is input from this forum of personal experiences - prats and pitfalls, your personal history with tanks, which method of fuel transfer do you prefer, etc., etc., etc.
Opinions are very welcome, but please try to back them up with facts and/or experiences.
First - a few basics that apply to either style of fuel transfer. If you know of additional facts, please post them. These are here because these physical traits affect fuel transfer.
1. Fuel Expands under heat. In some cases, dramatically so. The design has to be able to deal with the expansion of the fuel. This is done by a vent opening on the aux tank that allows expanding fuel to escape.
2. Expanding fuel builds pressure if not allowed to escape. This is NOT a desirable trait.
3. As the fuel is transferred from the aux to the main, the volume of fuel moving from the aux tank must be replaced with a similar volume of air from the atmosphere. This is accomplished by the same vent hole. See #1.
4. And while obvious, I'll put it here - there must be ROOM in the main tank for the transferring fuel to go - and the air in the main tank must be able to vent out as it is displaced by incoming fuel.
OK - Let's do a basic examination of gravity feed:
(This is kind of a 'brain dump' for me - I'm just kind of thinking via my keyboard)
Gravity pulls DOWN. Liquid will always flow to the lowest point, as it is pulled there by gravity.
Logic - a gravity transfer tank will need to be mounted in such a manner that the fuel exit (and level) of the aux tank is HIGHER than the fuel entrance (and level) of the main tank. This way, when then valve is opened, the fuel will flow from HIGH to LOW.
Flow rate equates to time. Faster flow rate = less time, slower flow rate = more time.
Logic - the larger the inner diameter of the fuel lines, the faster the flow rate. The greater the differential in elevation (we're talking inches here, folks !) the faster the flow rate. (Very minor difference, unless you were to mount the tank on some sort of superstructure 6 feet above your head :blink: )
Gravity is always present. (Unless I missed the event, I've never noticed it leaving.)
Logic - does not require mechanical assistance.
Flow DIRECTION is dependent upon gravity -
Logic - Fuel flows from high to low. (redundant, I know. but very important. )
And Pump feed:
Simple - a fuel pump is installed to transfer the fuel REGARDLESS of tank elevation differentials.
A fuel pump could be used on a tank that might otherwise function as a gravity feed tank.
Logic - using a fuel pump allows the placement of the aux tank to be agnostic in elevation to the main tank. (does that make sense?)
Fuel pumps require electricity - or a gerbil on a wheel, whichever you choose.
Logic - this is a failure point.
Fuel pumps produce pressure -
Logic - fuel lines and fittings must be able to accommodate the increased pressure.
Fuel pumps vary in flow rates (usually listed by pressure)
Logic - it is possible to install a pump with TOO MUCH PRESSURE and make a huge mess of your garage when the fire department puts out the resulting conflagration.
Some fuel pumps can burn out when operated dry.
Logic - research what you buy. This is not a component to save $$ on.
And now to fuel transfer differences - and this is from my personal experience.
Gravity feed - I have limited experience. I installed a gravity feed tank last November, which was quite a learning curve for me.
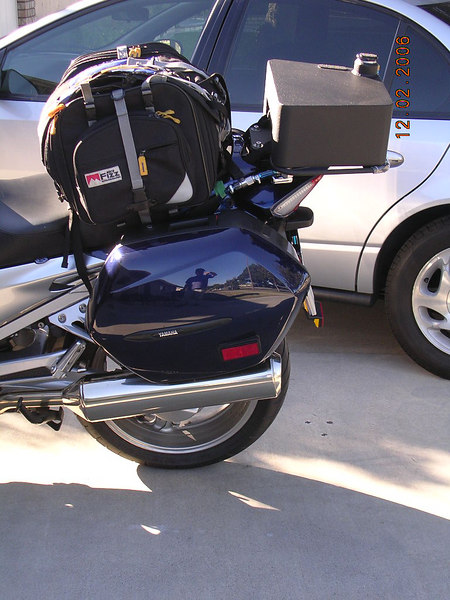
This tank was on my bike long enough to run three fills through it. If you notice, it's much higher than a pillion mounted tank - and the transfer rate was relatively quick, due to the large differential between fuel levels. (The bottom of the aux was higher than the top of the main) It was possible to open the petcock, and have this tank empty through the main tank overflow valve if I wasn't watching the main tank level. This meant I really had to pay attention, and make very sure that the valve was closed when I filled it. So - I found myself riding along, trying to remember if I'd closed the darn thing! The petcock was not easily accessable when riding - I had to stop the bike, then twist backwards, and open the valve. I simply could not do it while underway. This could be dealt with by a different fuel line routing, perhaps an in-line valve for the transfer. The fuel movement inside the tank was very noticible - sitting up high like that, any wave motion was amplified. I overcame this by installing anti-slosh foam in the tank as per IBA regs. Should I elect to use it again, I will also have to engineer a proper static ground for it.
I have no personal experience with a "pillion mount" style of tank. Many of my fellow riders do, and I look forward to hearing of their experiences.
Pump feed -
I installed a "underhung" design, as I had discussed with Ron Sampson his need to adapt the long standing Ron Major design to the FJR1300. He used my bike as the mule for this - and I worked with him extensively to get the system 'tweaked.'
IMHO -in retrospect - I should have gone with a pump to begin with. I could still rig a pump on my gravity feed tank, and not have to deal with the valve position.
Using the pump feed I find to be substantially easier. I can simply turn on the pump via a LED (visual indication) rocker switch on my cowling, and inside of 25 minutes, 4.3 gallons of fuel transfers to the main tank. I think the ability to pump the fuel easily with a minimum of fuss is of benefit. This transfer time could be improved upon, as I used 1/4" line and fittings. This is due to the tight radii that I needed to obtain with the line routing. The 5/16" line simply would not make the turns without collapsing.
The installation of a fuel pump is more complex - wiring, fusing, additional fuel lines, etc., but it's certainly not above a reasonably competent wrench. If you've got the self confidence to do the main tank penetration, the rest of the installation should be easy. If you could install a gravity tank, you could install a pump.
The downside? COST. As there are more components, the cost to install a pump is greater than gravity feed.
I did the final install last May - and have now put just over 7K miles on it. It has functioned as designed without any problems. I continually check the nuts and bolts, I check for abrasion on the fuel lines, leaks on the Herbie clamps, etc. But so far - it's been bulletproof. Time will tell.
So - that's where I'm at - I have heard many additional comments and stories from forum members - but not having matching experiences, I can't relate those to you.
Pump vs. Gravity? Well ?