ionbeam
2 FUN
As I understand the charging system, the FJR has a stator and shunt-regulator/rectifier. Unlike an alternator or series controlled (blocking) stator, the FJR stator supplies its full output at all times. If the power is not used by accessories, it is shunted to ground by the switches in the R/R. If the power is all consumed by accessories and bike loads, the stator works no harder, you just enter a net discharge scenario. If you are running no accessories the net surplus power is shunted to ground which has no effect on the stator, but does create heat in the R/R and may increase heat in the stator.
What am I missing?
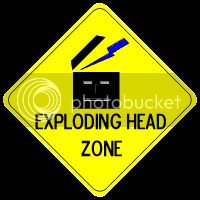
The issue is voltage drop.
The Gen I electrical system is designed to maintain 14.x volts up to 490 watts of power consumption (35 amps) and the Gen II should maintain 14.x volts up to 590 watts (42 amps). Once the electrical system draws more current than design, the voltage starts to drop. There is a fundamental voltage, current, load (resistance) law of electricity (Ohm's law). The values react in specific ways such that in the case of increasing load, current will go up but it forces voltage to go down.
Riding along with the DATEL showing 14.0 volts the R/R is shunting excess power to ground. Turn on the driving lights, the R/R stops shunting power to ground because the electrical system is consuming ALL the power generated, and the stator can just maintain 14.0 volts. Now turn on the heated grips. Voltage on the DATEL drops to 13.4 volts, the R/R is off allowing 100% of the stator's output to pass. Where did the voltage go? There has to be a voltage drop someplace. The voltage drop happens in the stator; the stator trades voltage for current. The byproduct of this drop is heat increase within the stator proportional to the voltage drop, or conversely said, heat increases proportional to the current increase. The heat is generated in the stator windings and concentrates where there are wire connections or wire insulation break down. This is why the Electrosport stators almost always show failure in the same place -- where the stator winding wires bond to the wires that exit out of the stator at the top lobes of the stator core. The lower the voltage goes the more heat that gets generated within the stator. The voltage drop is most accurately measured directly on the output pins of the R/R to eliminate and voltage drops caused by harness connections. The lower the voltage at the R/R output the hotter the stator runs.
I'll give this explanation a rethink tomorrow after our Parker's Maple House breakfast run and clarify this if needed after that.
Last edited by a moderator: