
[SIZE=12pt]A Visit to GP Suspension[/SIZE]
[SIZE=10pt]Matt Watkins (aka Ignacio)[/SIZE]
One of the benefits of working in the same office as the venerable, constructive, and sometimes curmudgeonly Warchild is that you are privy to the inside scoop on his unique way of dealing with the cold winter months...which is of course....him setting up Group and Self Buys.
I've certainly taken advantage of them myself with a Wilbers on a GB bout three years ago and again on one two years ago. So, wandering down to Dale's office on Thursday the conversation turned to what he was doing on the Friday off.
Sometime in January Warchild says, "I'm heading down to Portland to take some pictures of GP Suspension and have them do a rebuild on some Blackbird parts."
It was about 4 seconds of pause and he adds, "Wanna come?"
I said, "Hell Yeah!" and I even offered up the Jetta as the cargo rig. And by 10:30 Saturday we rolled into Oregon City and found the shop in an area industrial park. Dave, the owner, greeted us in a cluttered front office that I've come to learn is a mark of creative inventor types. Various parts strewn around in seemingly haphazard piles, but the kind of nuanced piles that one knows have stories.
Tour of the Shop
By the way, every wonder what $14,000 worth of shocks looks like in one box? Their delivery from Japan was surprising as there was hardly any packing material.
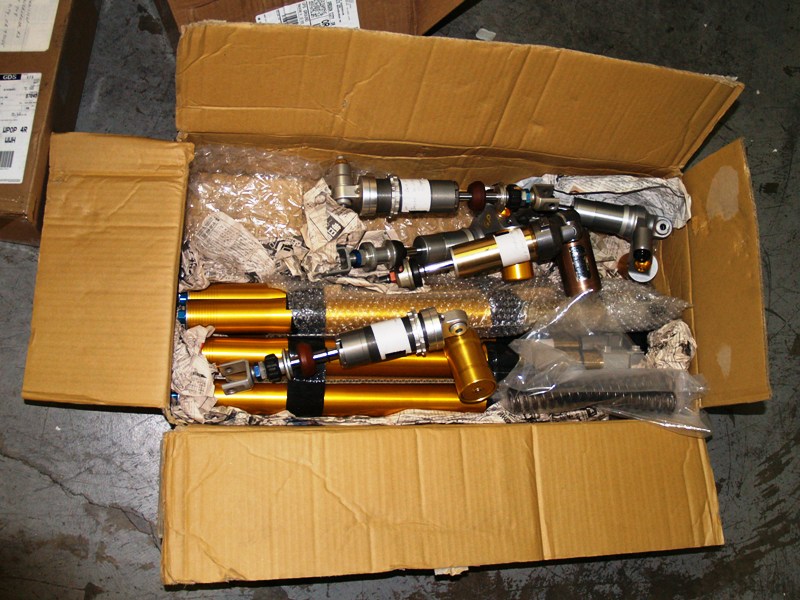
GP Suspension only does motorcycle suspensions and over the course of a few hours I learned that there are a lot of "stoner dudes" calling up looking to have air ride suspensions installed in their '70s POS Cutlass Supremes, "<ring....ring> Hello?. Ummmm......sorry, we only do motorcycle suspensions. <click>"
I should also point out that every time a person calls.....it's time one or both of these guys aren't working on getting shocks done. They did remark that the most recent Group Buy had been a bit easier since Warchild had put the fear of God into them to not call unless they absolutely need to. He also noted that Penske's slowness of delivering new shocks on what was overwhelming demand by the Group Buy had stretched some people's patience.
Here's a pretty good overview of the shop. The center of the process starts with a bin of forks and shocks on deck to be worked on, several CNC machines, and workstations around the perimeter.
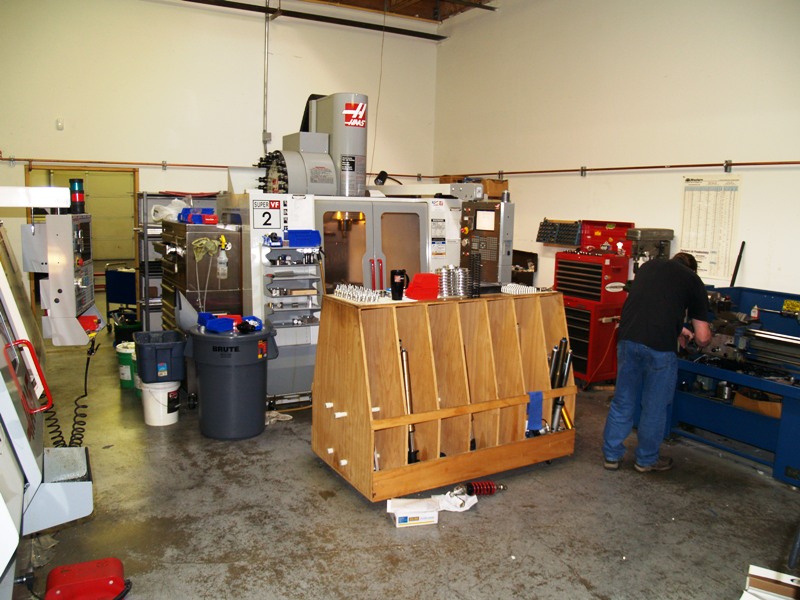
Walking past the box one enters the inner sanctum of GP Suspension...where the magic happens! First thing one sees is a magic CNC mill.
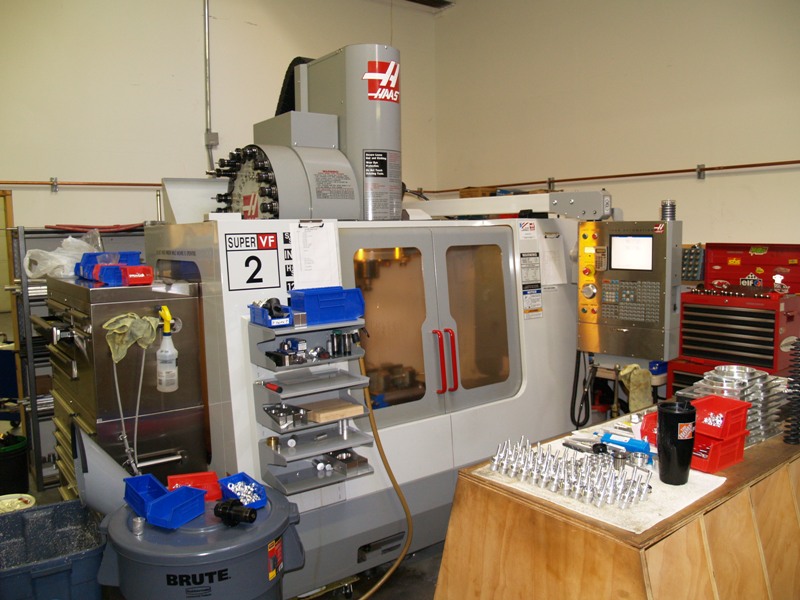
This machine runs high 5 figures in cost and turns blocks of aluminum (usually 7075) into smaller chunks of aluminum with threads, holes, and other highly function gadgets. Another similar machines is a CNC lathe with a powerhead. The owner tried to explain the details, but suffice it to say for round things it's more efficient than a mill.
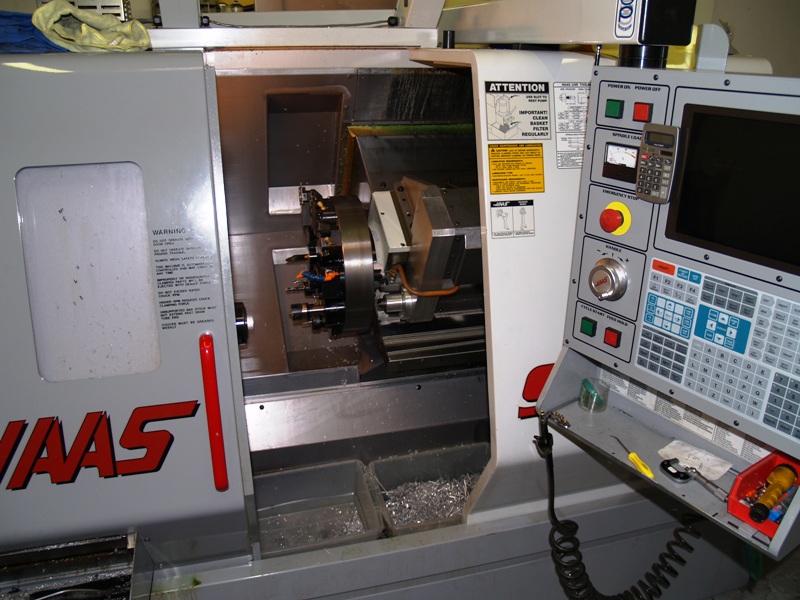
That machine makes the little critters below. What is interesting is that a long rod of aluminum makes one of them in about 2-3 minutes, chops it off, advances the bar, and makes another one. They're not complete as the part is then put in a machine backwards and more metal removed, but it's clear a finished part is not far off.
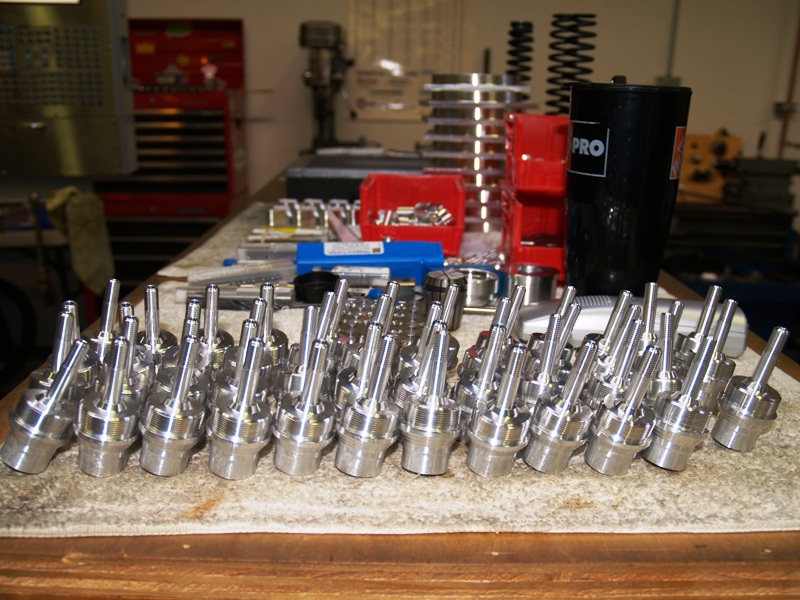
Wandering the shop one finds that toolboxes bought from Costco don't have things like tools in them. Wandering through drawers ones finds finished compression needles, compression dampers, etc. Common tools are deliberately on pegboards around the shop perimiter for easier access.
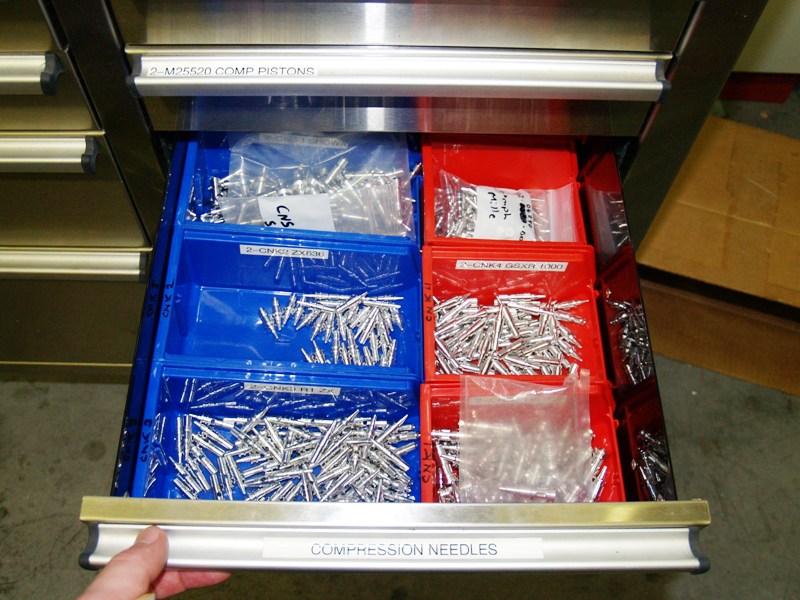
After about the third drawer I was largely baffled by all the mechanics of everything...and quickly reverted to a refrain of, "Oooh. Look at the pretty shiny thing."
And if I heard Dave right besides the hugely intricate and detailed machining procedures.....this rack contains two different aluminum alloys. One is the more tradional 6160 often equated with aircraft aluminum. They're the three shiny ones. The remainder of the tray is some other aluminum alloy number made with a portion of titanium...or maybe they're annodized. ......ooooh...look at the pretty shiny thing.
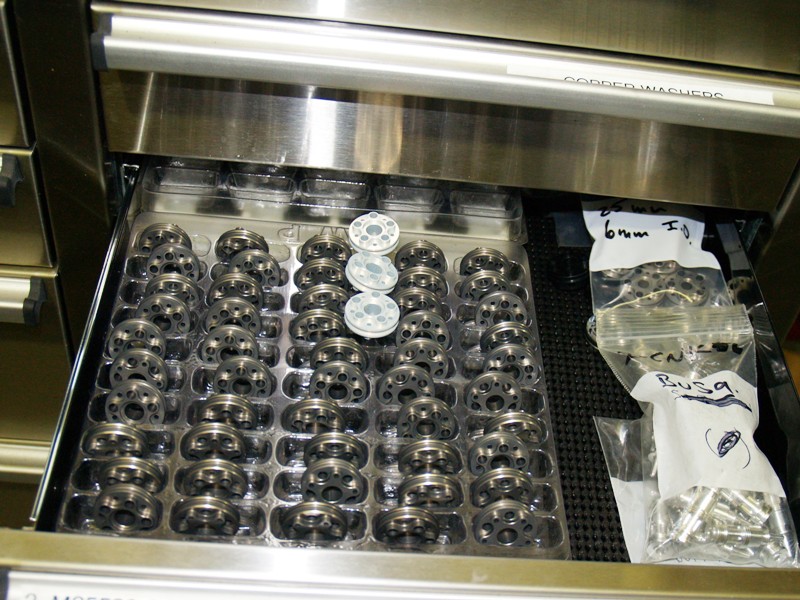
And one has to just love how sexy these two parts are. On the right is a stock part. On the left is a GP Suspension custom machined product with titanium color annodizing. Also, of note, those hex are made on the lathe with the power head. They're not made on the mill.
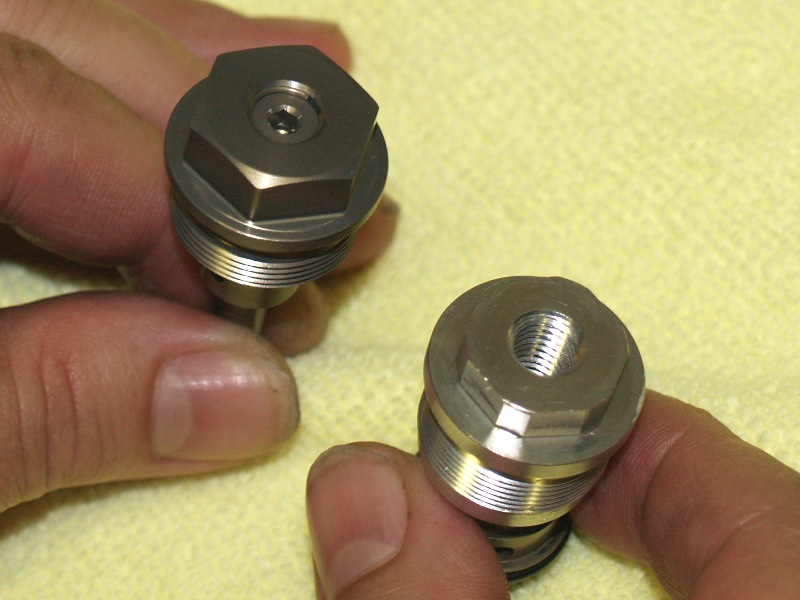
More 1/2 finished goodies:
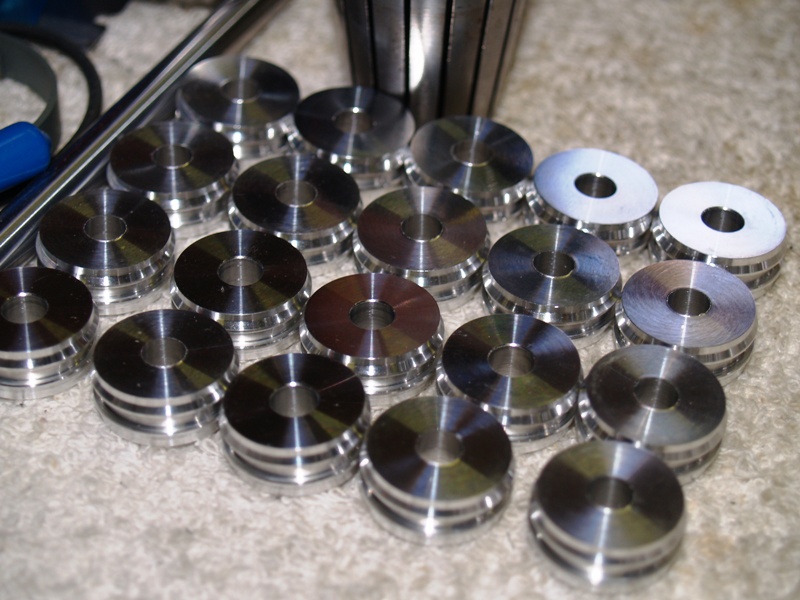
And anytime you're machining billet aluminum you're making little pieces of aluminium.
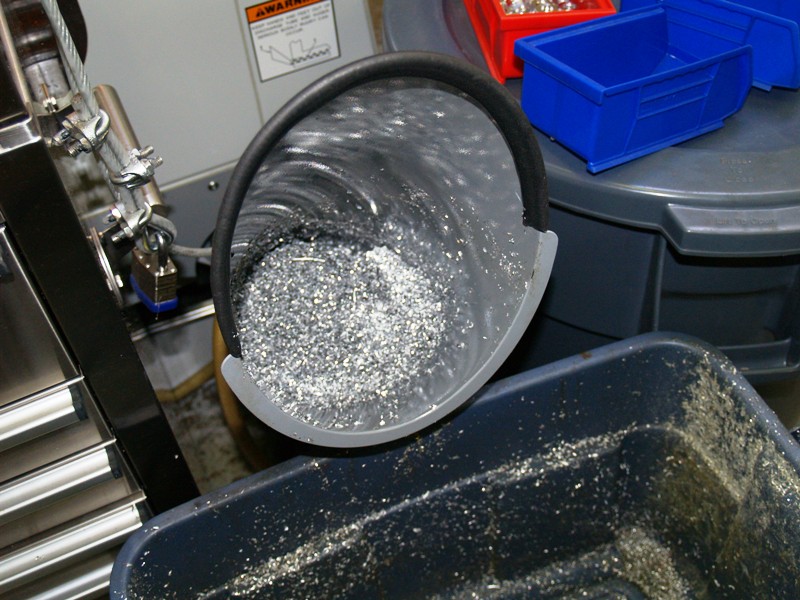
Fork Rebuild
Forks are disassembled and cleaned in a solvent tank with some custom mounts for holding various parts. In this case the subject is a set of forks from Warchild's Blackbird that did the world record Bun Burner GOLD Hell Week.
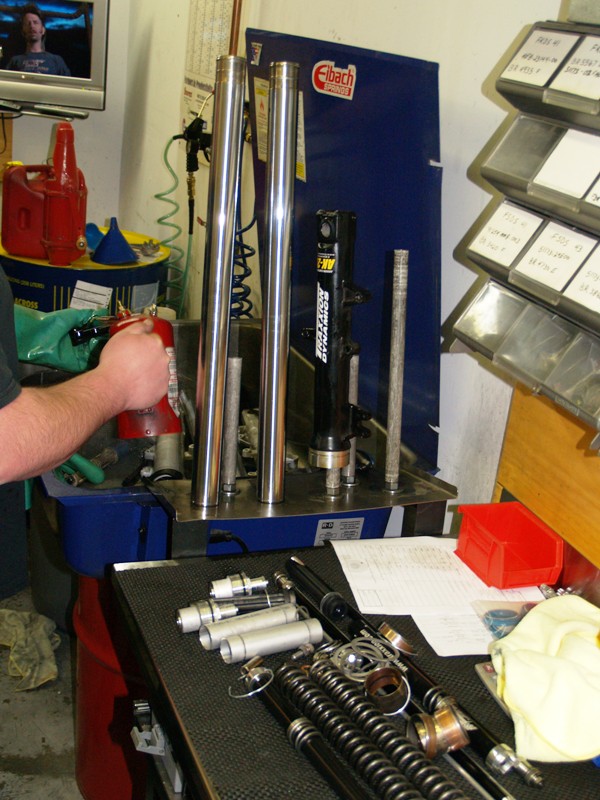
Parts are disassembled an cleaned in tanks
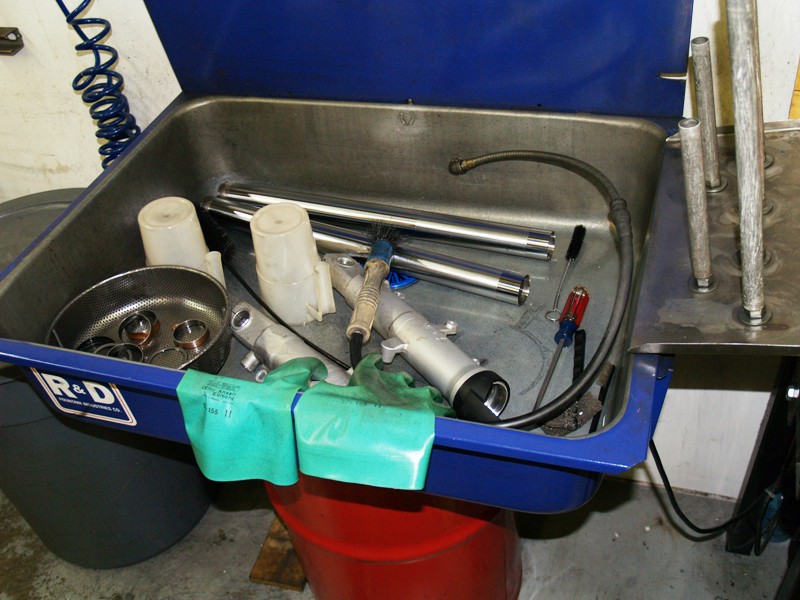
With contact cleaner that these guys buy by the 55 gallon drum, and put in spray bottles that work off compressed air, to say they're neat freaks is a bit of understatment.
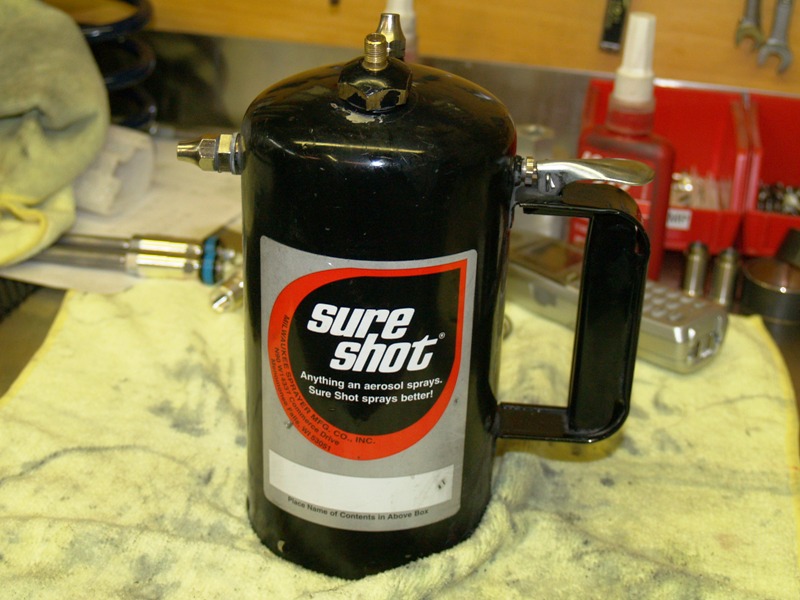
A gratuitous shot of an open fork that they explained something to me, but I've forgotten since the picture. One can notice how clean things are though.
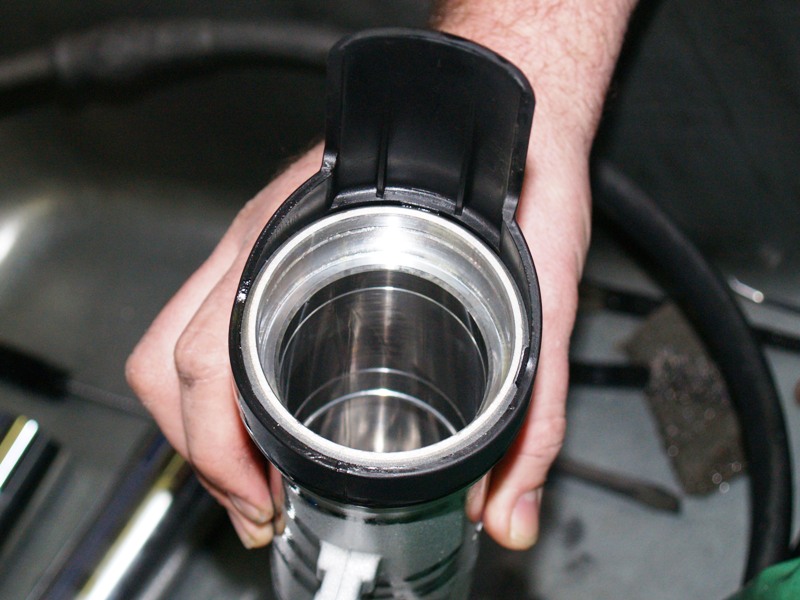
While Warchild's forks were being done he looked over a computer program the shop uses mostly for racers to keep track of elaborate things like shim stack recipes.
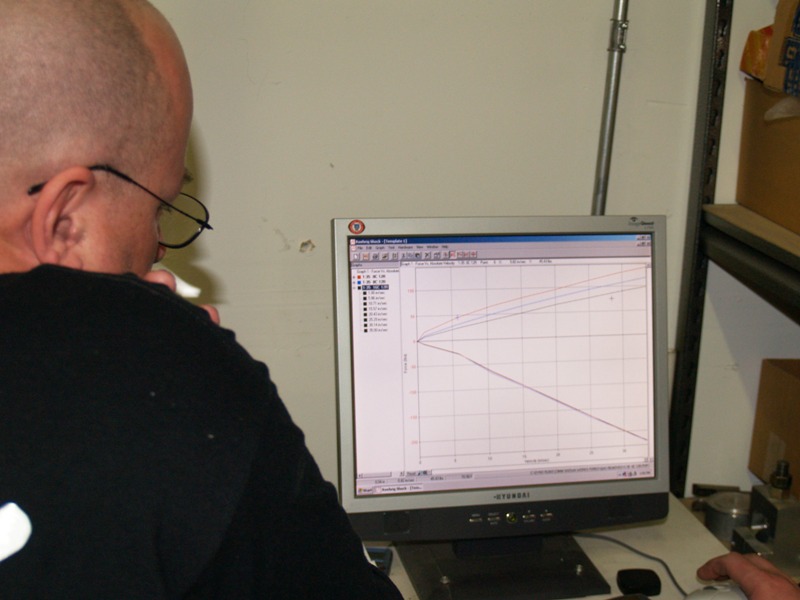
And to give one a sense of the amount of work these guys do...they have two drums for waste oil from the forks.
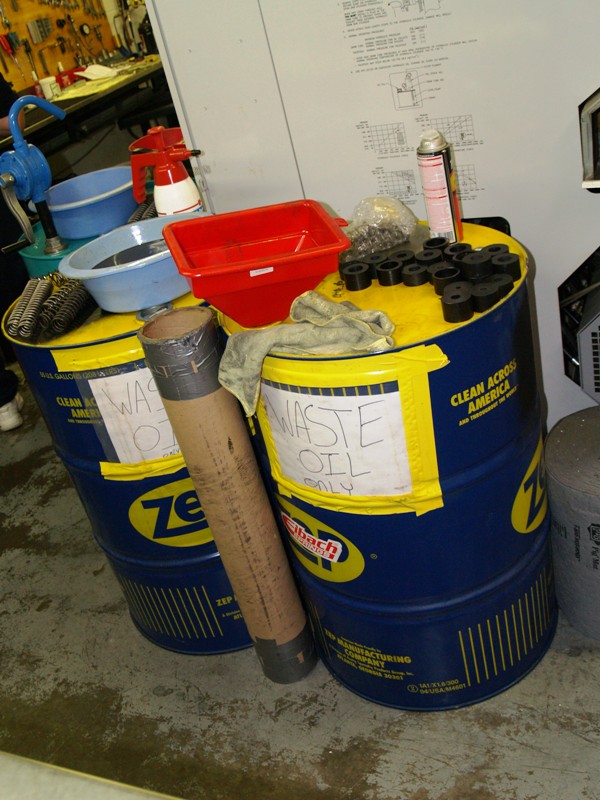
They also noted they had seen a trend on FJR forks. The Gen 2 bikes seem to rub through the teflon coated bushing faster than Gen 1 bikes. They don't know why, but thought that was odd with a supposedly updated design.
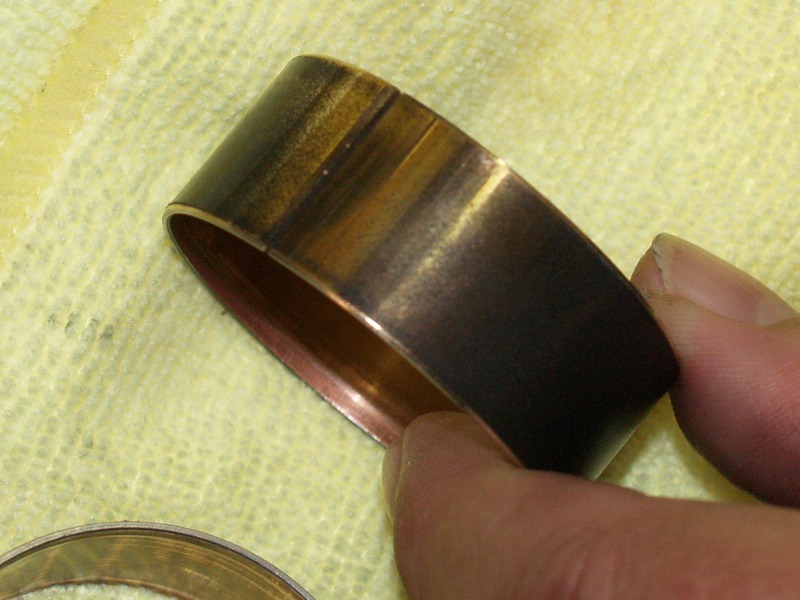
This what they're supposed to look like:
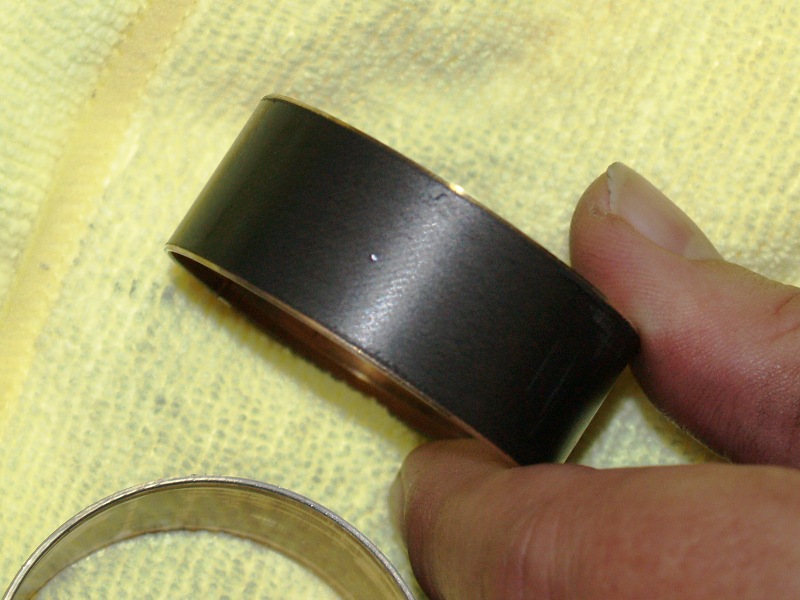
No matter. They keep a bunch in stock anyway for replacement.
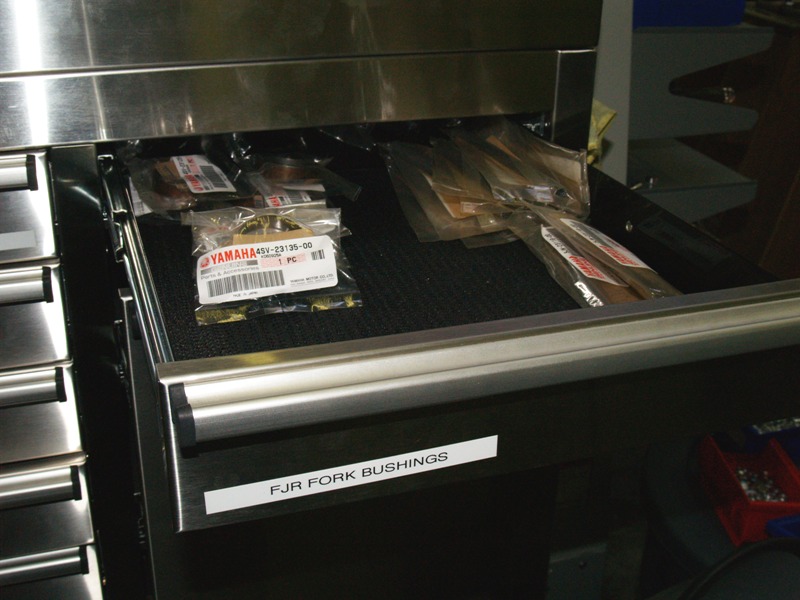
Besides a pegboard heaven of tools including many specialized parts..they also make some of their own tools. Here's one that actually is a cut down of an old fork tube IIRC. They use it's smaller diameter to seat a part inside a larger fork. Also in the previous pictures many of the racks and work tables are custom made.
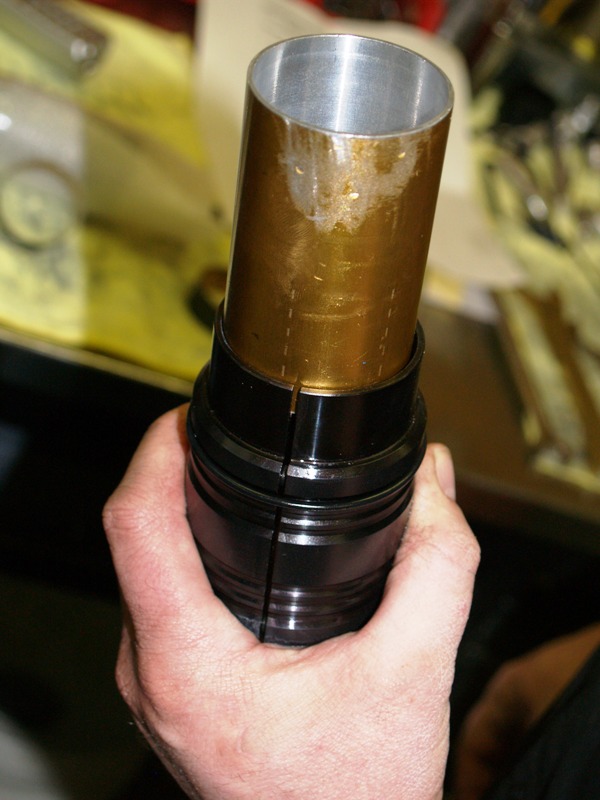
I sort of forgot to show a picture of a rebuilt fork, but suffice it they look pretty much the same in a picture as when they came in the door...only cleaner.
Rear Shocks
The rear shocks were fun too. These guys have a nice inventory of springs in assorted colors and weights.
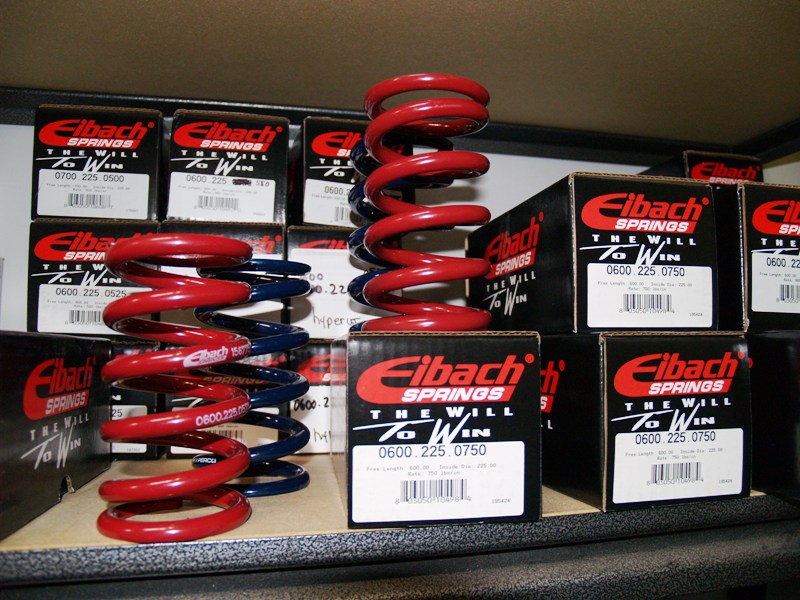
Here's a spiffy new spring on an Ohlins.....again likely a member of this forum's shock.
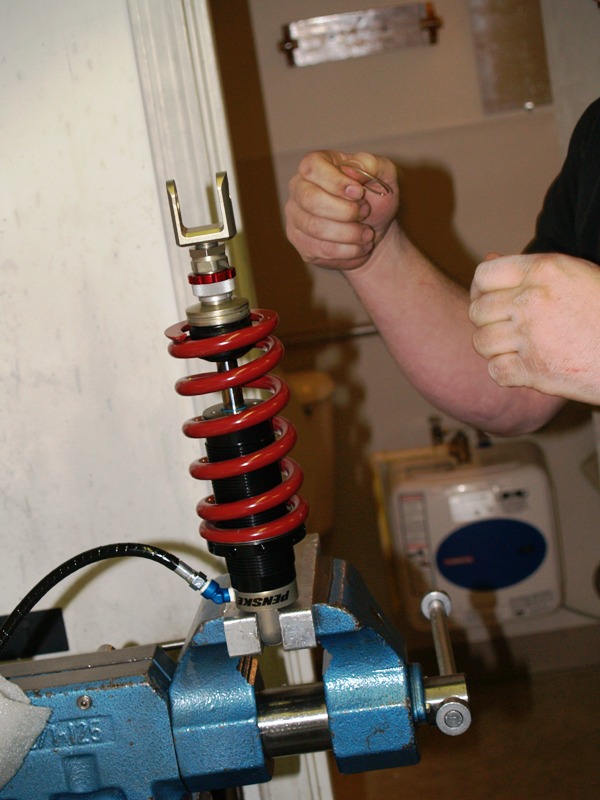
A close-up of another one of their little machinist tweaks of a vise. Special jaws, notches, and pins for even more shop-built gadgets are for various custom things they've learned and built over the years. Their inventiveness is artistic actually....with a large dose of practicality.
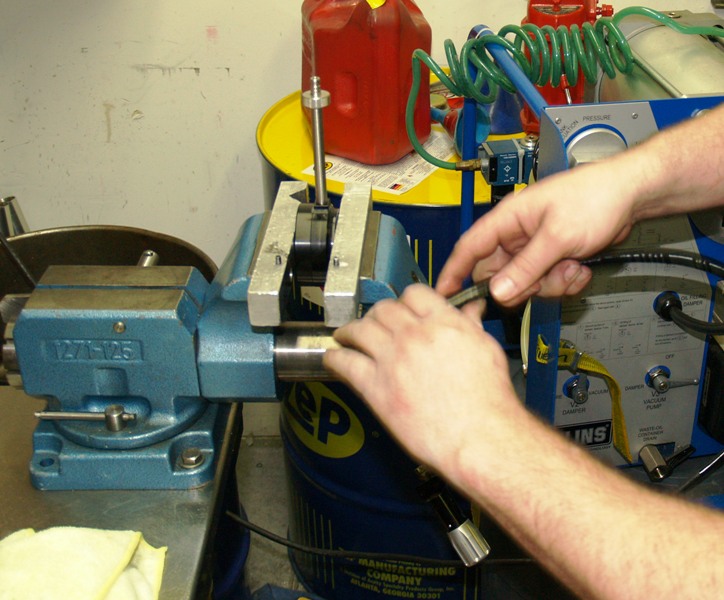
With one of the shocks torn apart he directed my focus on to the money-shot of where forks age, fail, and generally can be maintained. The outer seal and the inner seal (gray o-ring) get all matter of grime, grit, crud, and crap in them. They did suggest just hosing down this area of the shock occasionally would increase usable life.
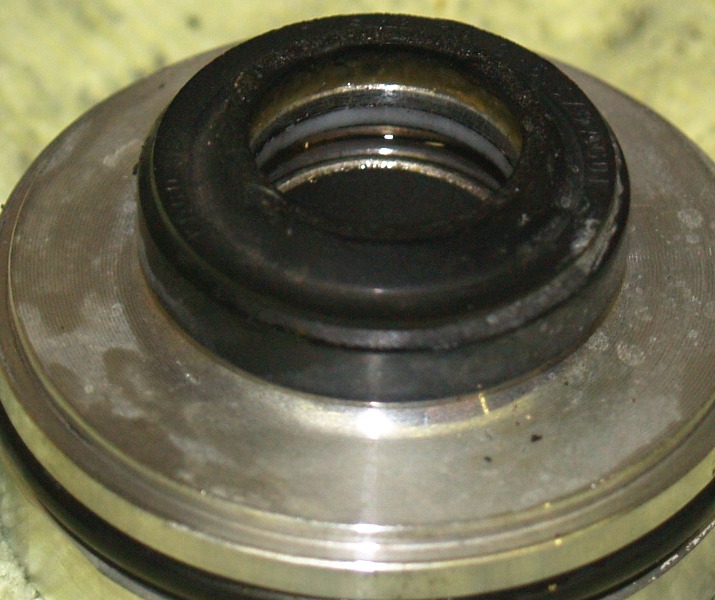
On reassembly they had a tub of uber whale jizz that even made these guys blush in price. A little dab goes along way.
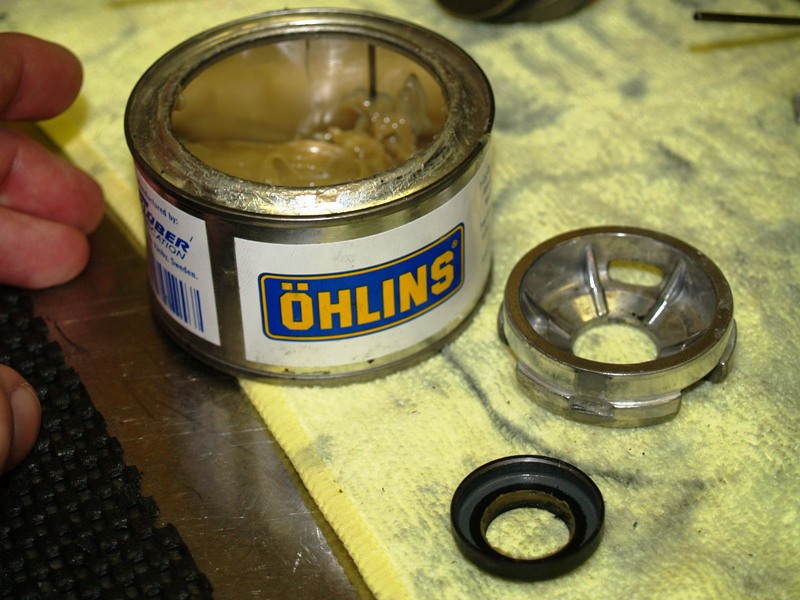
A stack of new shocks being prepped for you all! The paper under his hand has one of your names and data you submitted via the Group Buy website in 2007. See also the pegboard of tools in the background.
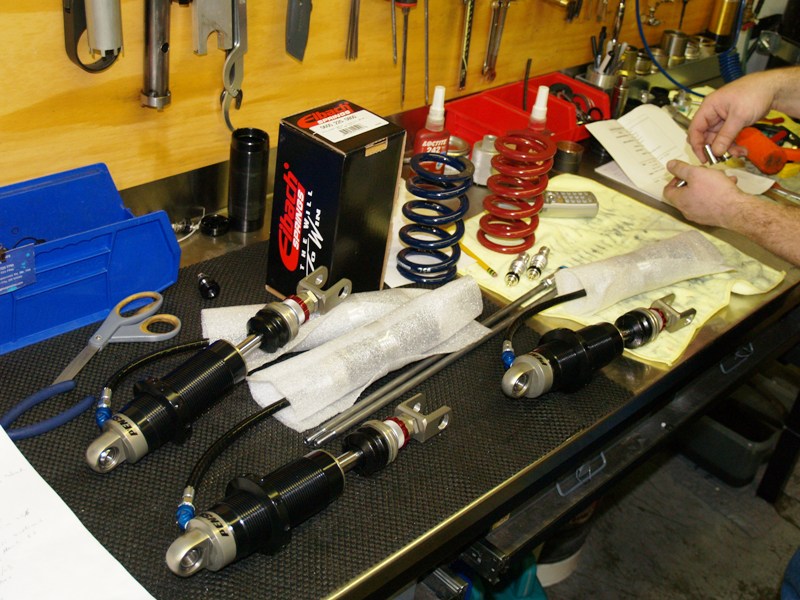
A good pause point and realize that to do good suspension work requires that a DVD be constantly playing on a 14" TV with tinny speakers. I had to give them props that Firefly was in the stack.
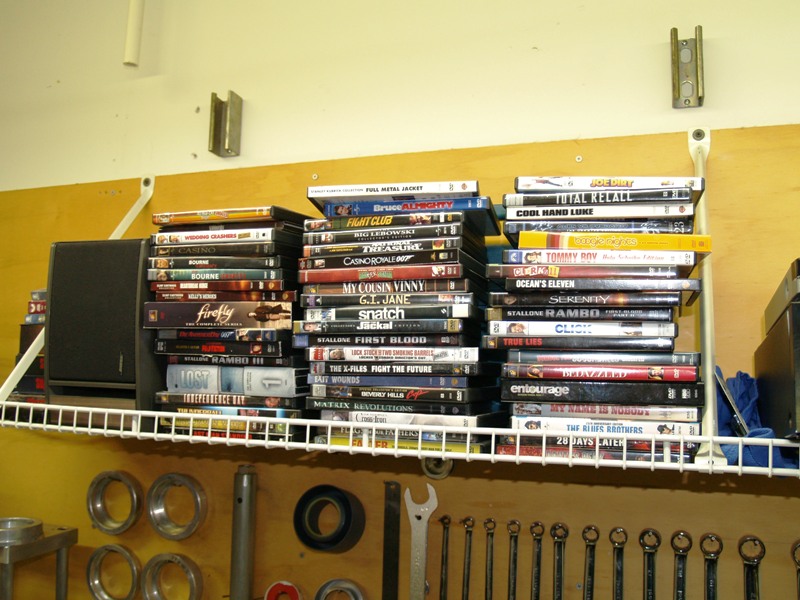
Also, completely unrelated to the task at hand, but surprising was that they had a lost parts bin. Not a big one mind you, but this tiny little box of parts that are the sum total of a shop that does many, Many, MANY suspension jobs each year. Hell I probably have more than this in my sofa.
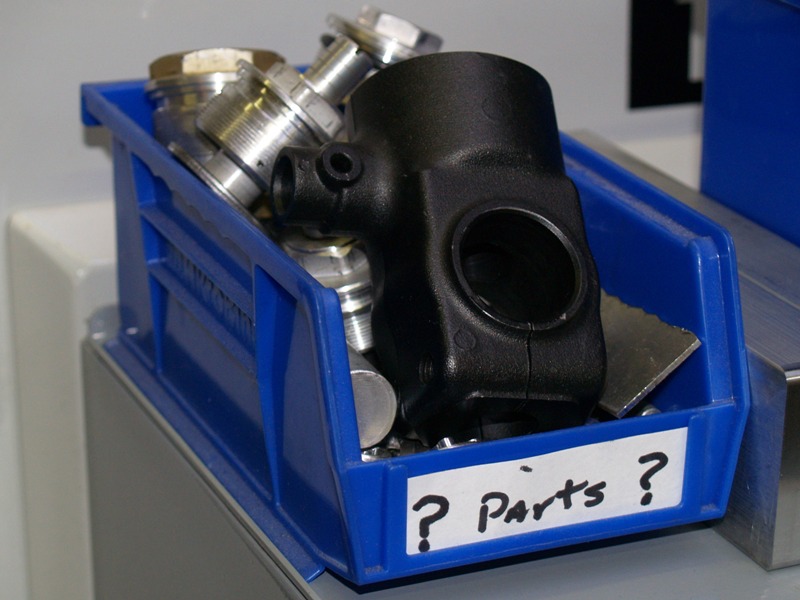
Back to the shock process, here's a Wilbers being rebuilt. They thought they were better than stock, but nowhere as cool as the Ohlins or Penskes with remotes. (note nitrogen tank in background...used in the next picture)
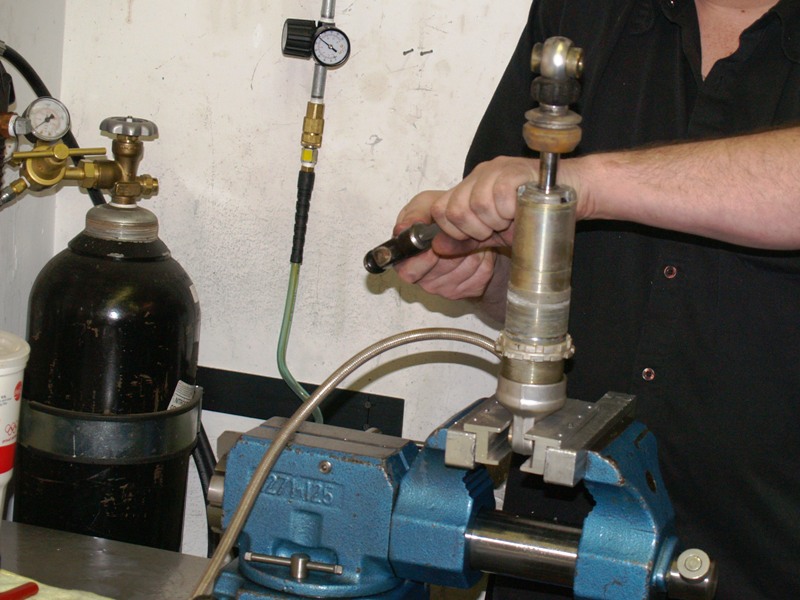
Here's another uber-spendy gizmo you won't find in a garage. They're 5 figures new, but they scored one for 4 figures (IIRC) after a tradeshow. Basically it's a suck and blow machine that charges shocks. It also sounds and looks like it should be in a hospital intensive care unit and not in a shock shop.
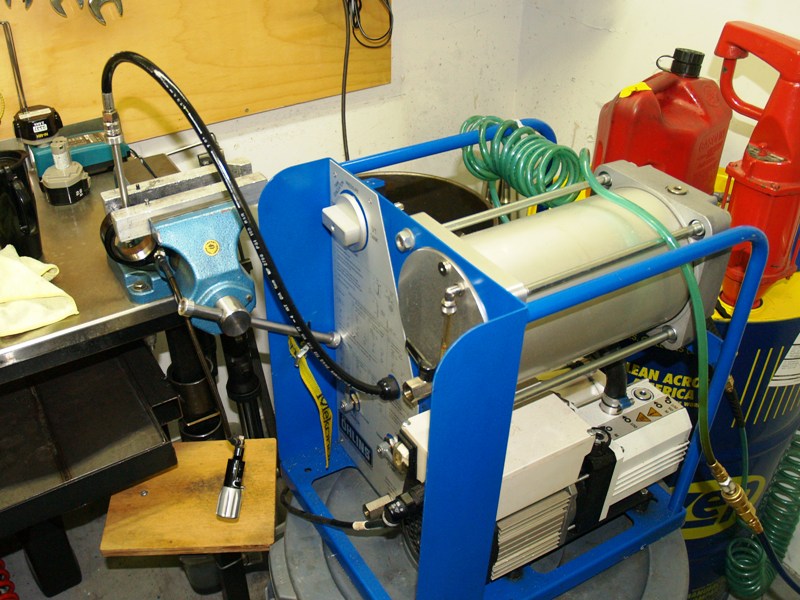
Shipping
So, after a fork and shock are complete...they go to the shipping department...which is on the other side of the bay.
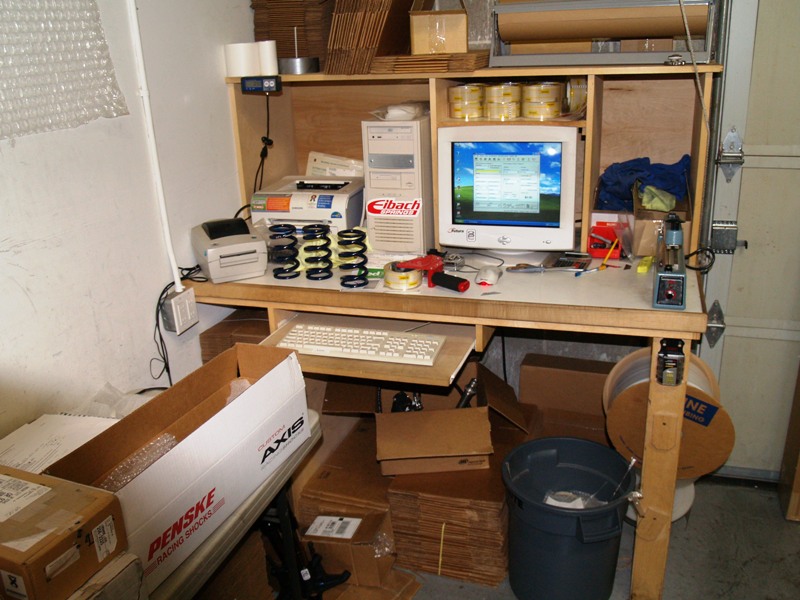
And another two forum members get their Group Buy booty shipped via UPS.
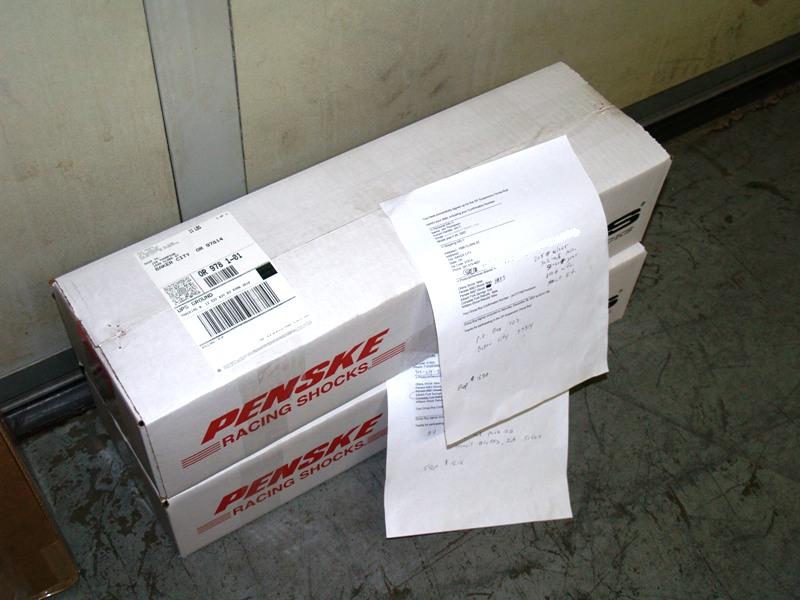
Follow Up
Following up write-up I learned that they purchased a new state-of-the-art CNC lathe with dual spindles. A Morie Seiki NL2000.....which sounds a bit like the Binford 6100 to me.
This means they can do front and backside machining in one operation and more easily keep up with production.
All I can say is "Ooooohhhh.....ooooooooh......Aahhhhhhh.......ahhhhh!"
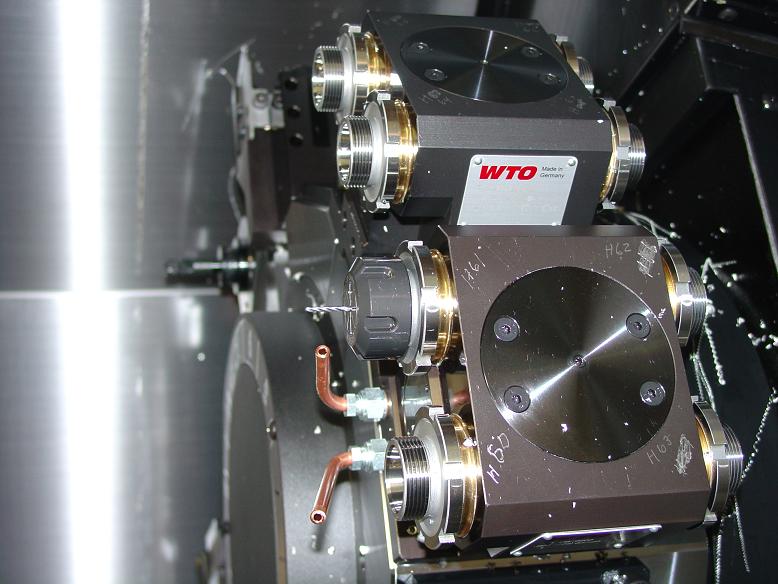
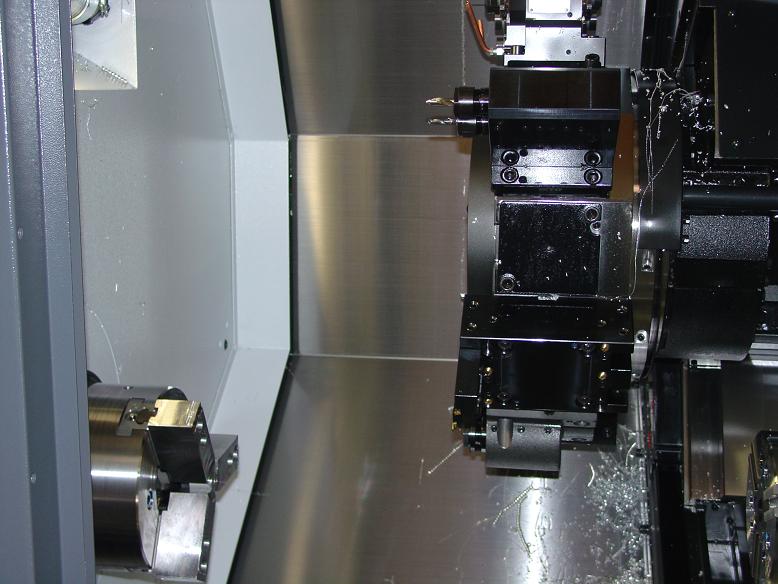
Last edited by a moderator: