scootman286
Active member
Happy Holidays to you all!
I have made some HiWay pegs for my 2007 FJR A model. I need some help finding some bolts I need to bring it together and thought I should ask the crowd for any input about where to get some metric hardware.
I need an M12 x 1.25 x 70 (or longer) Countersunk Flathead screw. I found some M12 x 1.75 but obviously, that won't work.
Anybody know a good source for bolts? I have stumped a few houses already so I hope I won't have to cut one myself. I figured I could maybe get an M14 in whatever pitch and then cut it down to the M12 x 1.25 with a die.
Here are some pictures of what I have come up with, any feedback (good or bad) is always welcome.
The top bolt will require tapping the frame to accept the 1/4-28 bolt (anti-rotation and some strength)
They will mount on this bolt (front mount bolt) and be angled to align with the opening in the plastic.
I have made some HiWay pegs for my 2007 FJR A model. I need some help finding some bolts I need to bring it together and thought I should ask the crowd for any input about where to get some metric hardware.
I need an M12 x 1.25 x 70 (or longer) Countersunk Flathead screw. I found some M12 x 1.75 but obviously, that won't work.
Anybody know a good source for bolts? I have stumped a few houses already so I hope I won't have to cut one myself. I figured I could maybe get an M14 in whatever pitch and then cut it down to the M12 x 1.25 with a die.
Here are some pictures of what I have come up with, any feedback (good or bad) is always welcome.
The top bolt will require tapping the frame to accept the 1/4-28 bolt (anti-rotation and some strength)
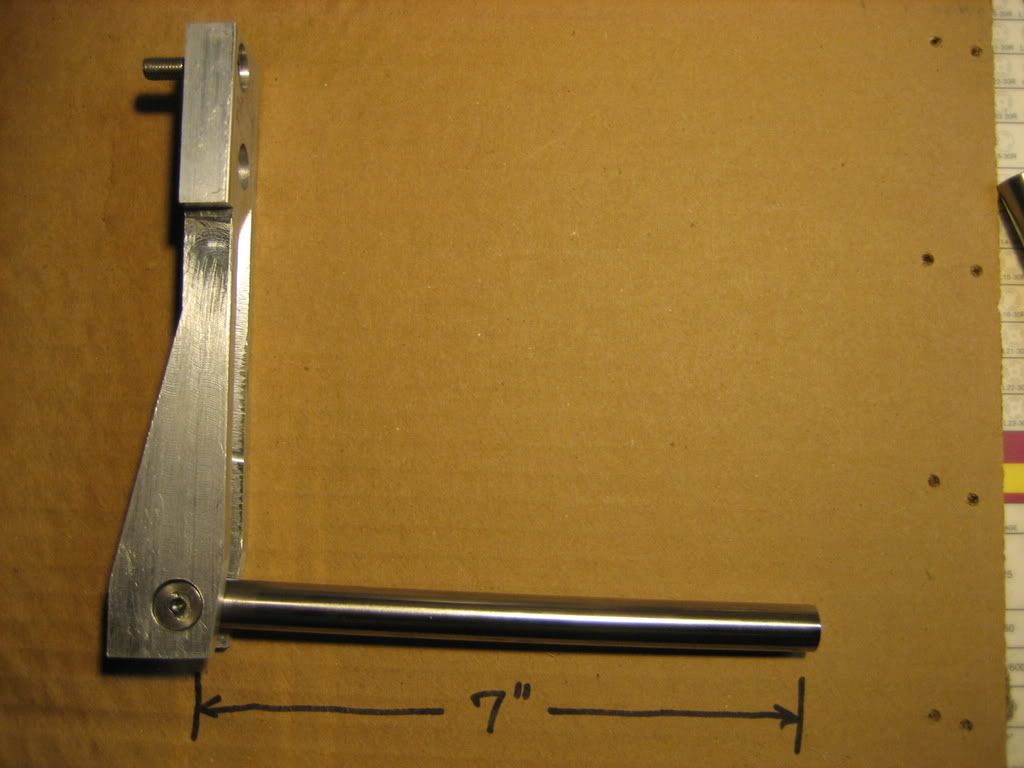
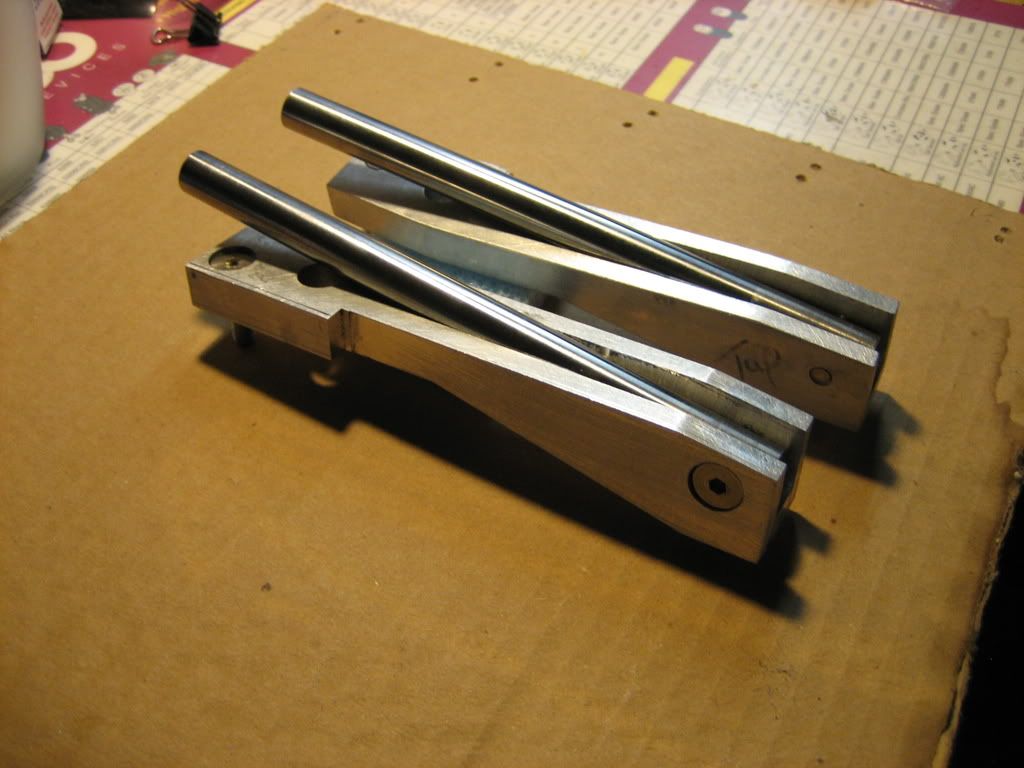
They will mount on this bolt (front mount bolt) and be angled to align with the opening in the plastic.

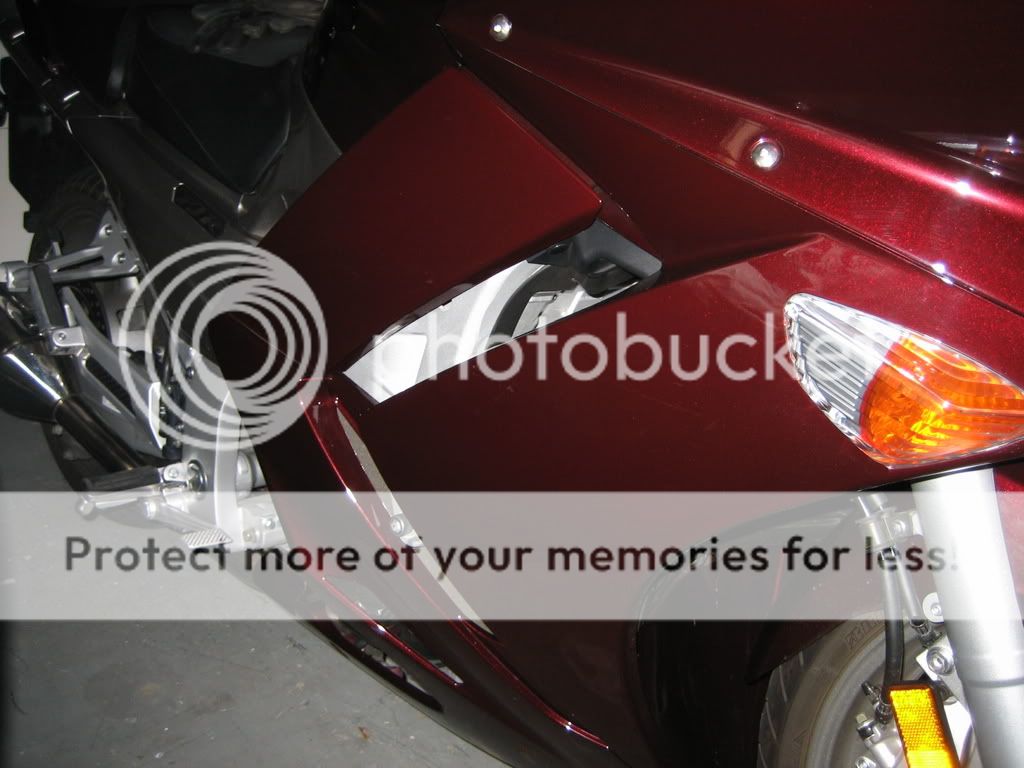