garyahouse
newbs need the forum
This summer a dream was born. I rebuilt the old shed into a stronger, larger, insulated, air conditioned and well lit workshop. Before it was even done, I purchased one, then another 1972 Honda CB350 twin(s). One was supposed to be a cafe racer, the other, a parts bike. Total investment, 1450 for the bikes, and maybe as much or more for the workshop. I'll try to post some pics of the workshop as time goes on, but for now, the first actual repair that I'm doing involves the rear shock mounts. It's an interesting story, but I'll talk about all that later. For now, just know that I'm no pro. I work with the meager tools and facilies that I have, and hope for the best. As the topic above stated, I'll be learning as I go.
So I finally began.
The shocks were held on by stripped out nuts. After removing them, notice the threads, or lack thereof... A wrong sized nut stripped off anything even looking like threads.
Below, I cut off most of the butchered threads, leaving a stub on which to lightly thread a nut to center up a drill bit that just fit inside the threads... in order to pilot drill the remainder of the factory stud. This keeps the drill centered.
After drilling it out to the right size, I threaded it to about 1/2 inch deep with an 8 mm tap...
Then after grinding off the last remaining threads, I measured up an 8 mm threaded rod and lock-tited it into the new tapped hole..
And finally, I put on a couple new washers and stainless steel acorn nut to finish the job. Multiply this times two, and now both sides are repaired and we can move on to the next item.
Stay tuned to this station for more of my backyard butcher block antics.
Gary
darksider #44
So I finally began.
The shocks were held on by stripped out nuts. After removing them, notice the threads, or lack thereof... A wrong sized nut stripped off anything even looking like threads.
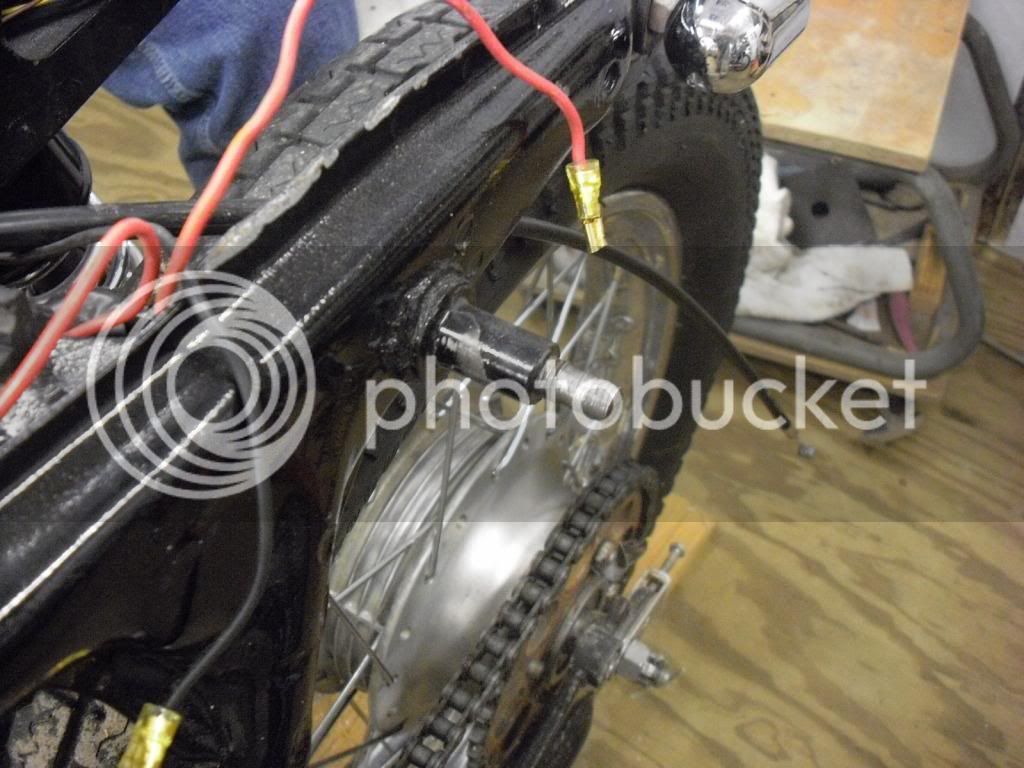
Below, I cut off most of the butchered threads, leaving a stub on which to lightly thread a nut to center up a drill bit that just fit inside the threads... in order to pilot drill the remainder of the factory stud. This keeps the drill centered.
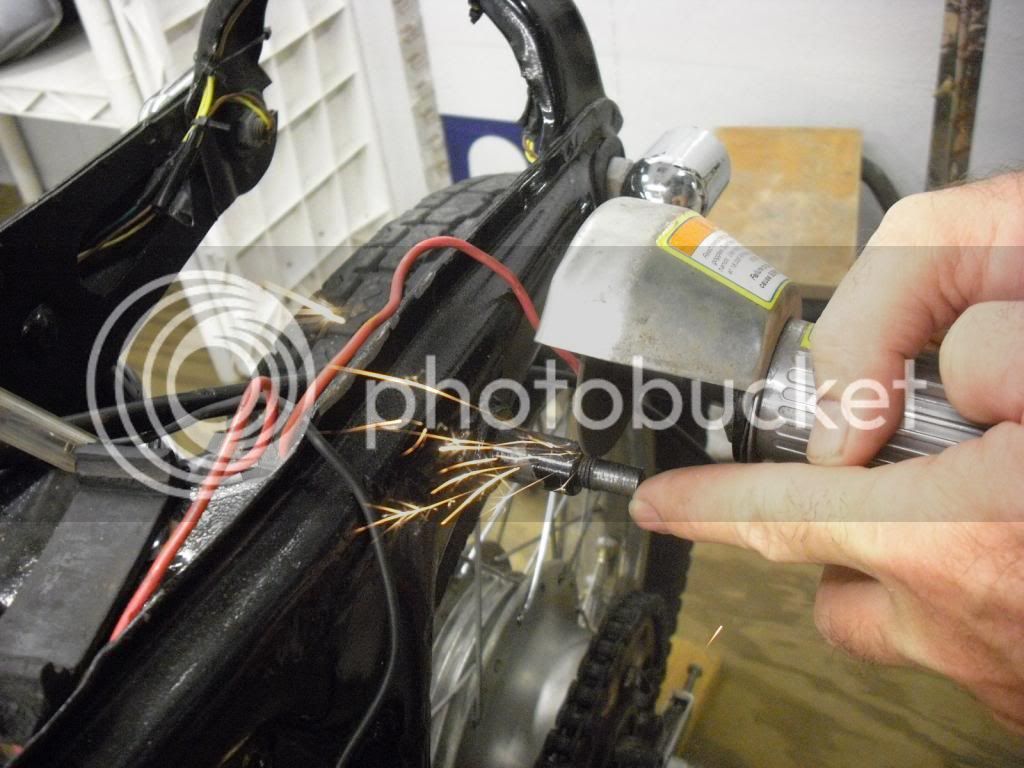
After drilling it out to the right size, I threaded it to about 1/2 inch deep with an 8 mm tap...
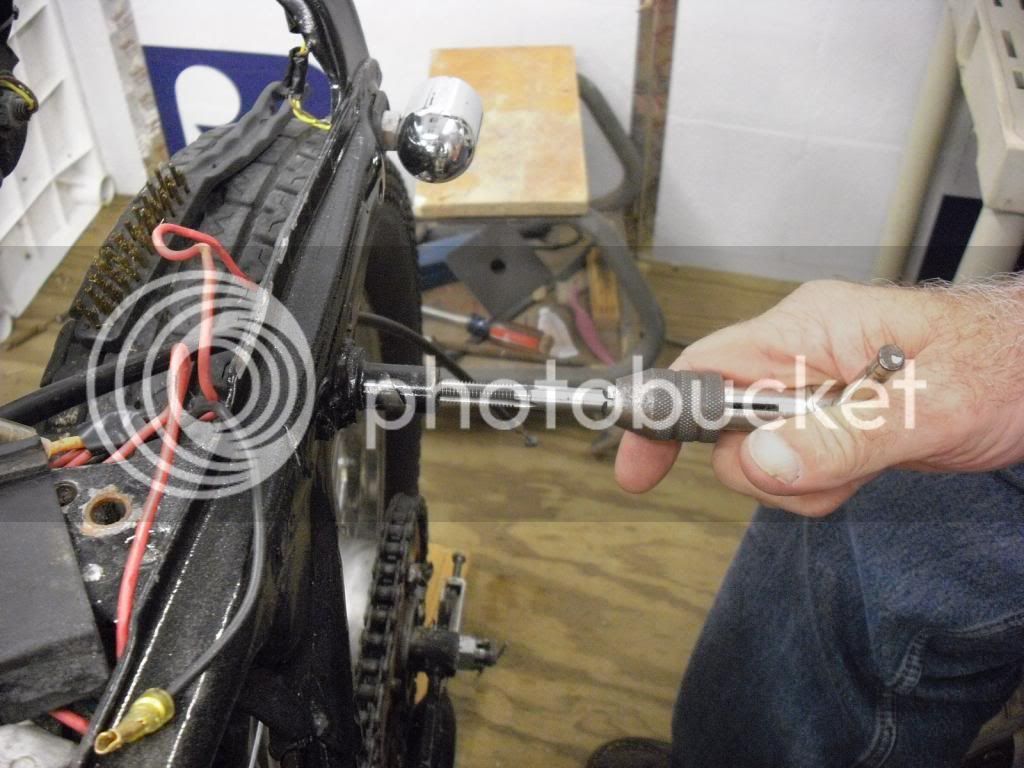
Then after grinding off the last remaining threads, I measured up an 8 mm threaded rod and lock-tited it into the new tapped hole..
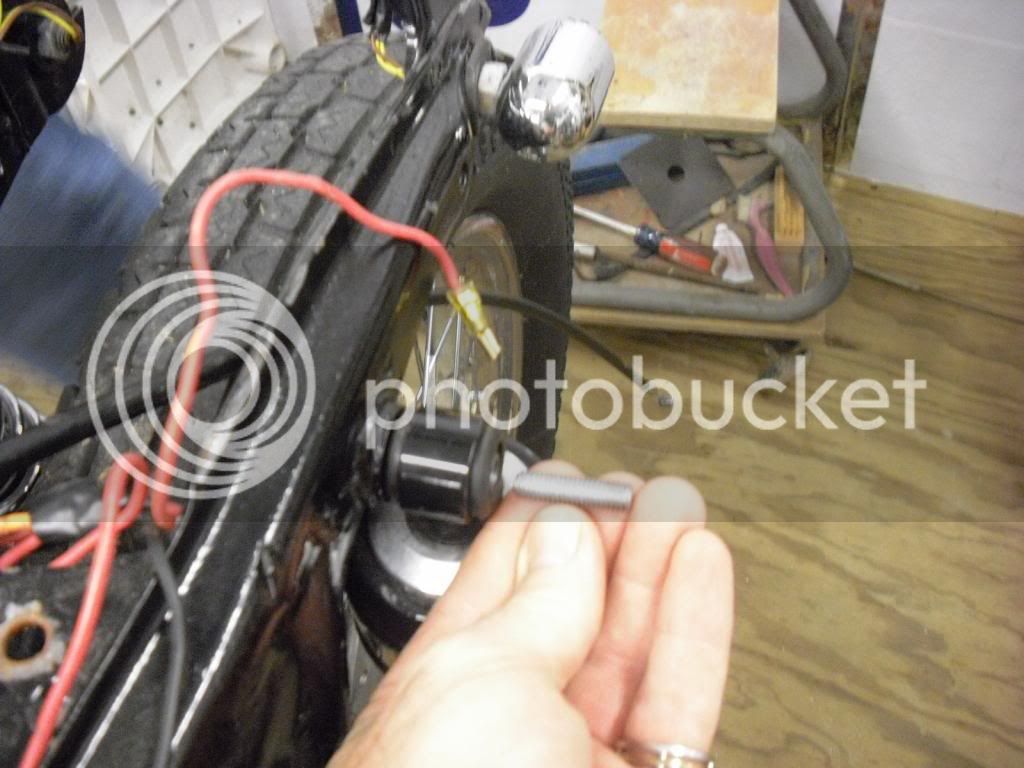
And finally, I put on a couple new washers and stainless steel acorn nut to finish the job. Multiply this times two, and now both sides are repaired and we can move on to the next item.
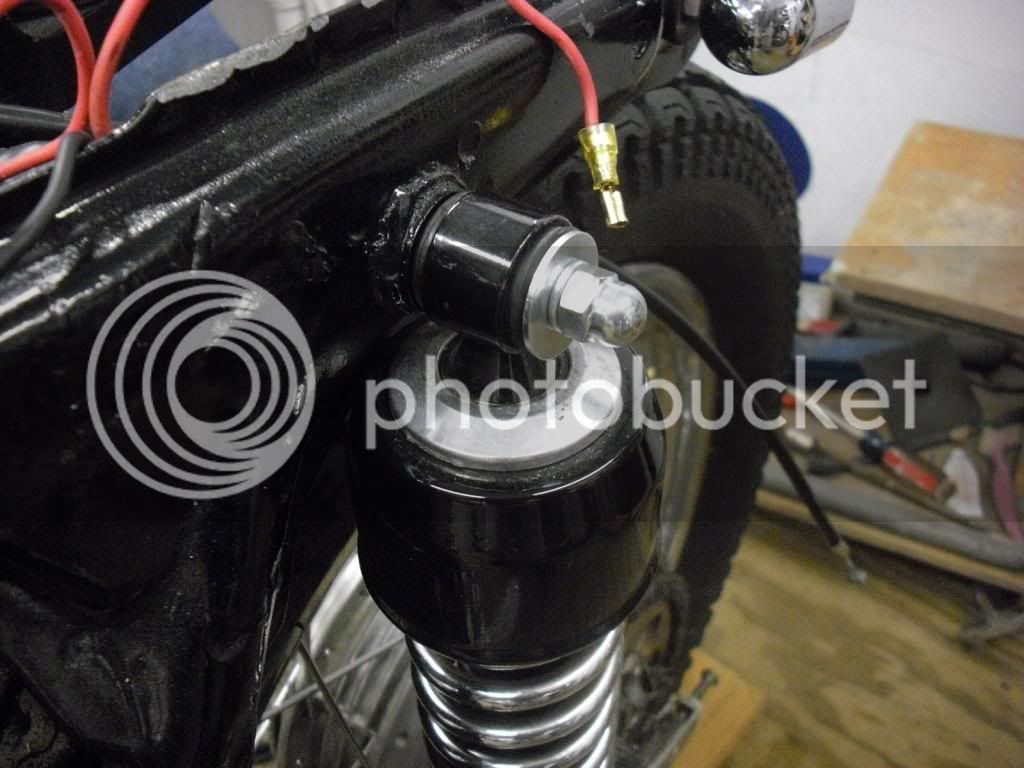
Stay tuned to this station for more of my backyard butcher block antics.
Gary
darksider #44
Last edited by a moderator: