ionbeam
2 FUN
Another little thing about installing any stator in the FJR, this quote is from a message during the first ElectroSport GB:
When I pulled the stator cover off my FJR I was shocked to see this groove cut into the rotor by the stator wire holding bracket.
You guys that had a squealing noise for a few minutes after startup now probably know what you were hearing. Hope your oil filter pulled out the lathe shavings.
Pay close attention to the stator wire retaining bracket and don't let it bend when you screw down the Phillips head screw. The ElectroSport stator has insufficient length (IMO) between the stator and the black feed-thru rubber gasket (rubber plug?). One intrepid person spent a few minutes working the rubber gasket further up the wires and had no problem getting the bracket to screw down without bending. It took me several tries, bending the bracket back into shape for each new try. I finally got it done with no interference problem. In my case I already had a groove cut in my rotor from Yamaha's original factory install.
In the following picture, shamelessly ripped off from beeroux without his permission – the nefarious bracket is up by the orange sealant, the bracket is held down by the big ol’ Philips screw. The offending part of the bracket is a small 'L' shaped tip at the bottom of the bracket, just out of sight in this picture.
Here is a compilation of text from different areas of my reply:Wasn't there an issue with the Electro Sport Stator scraping metal on initial startup?
When I pulled the stator cover off my FJR I was shocked to see this groove cut into the rotor by the stator wire holding bracket.
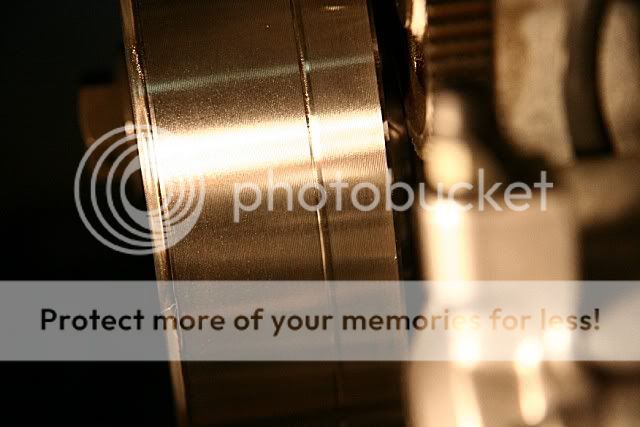
You guys that had a squealing noise for a few minutes after startup now probably know what you were hearing. Hope your oil filter pulled out the lathe shavings.
Pay close attention to the stator wire retaining bracket and don't let it bend when you screw down the Phillips head screw. The ElectroSport stator has insufficient length (IMO) between the stator and the black feed-thru rubber gasket (rubber plug?). One intrepid person spent a few minutes working the rubber gasket further up the wires and had no problem getting the bracket to screw down without bending. It took me several tries, bending the bracket back into shape for each new try. I finally got it done with no interference problem. In my case I already had a groove cut in my rotor from Yamaha's original factory install.
In the following picture, shamelessly ripped off from beeroux without his permission – the nefarious bracket is up by the orange sealant, the bracket is held down by the big ol’ Philips screw. The offending part of the bracket is a small 'L' shaped tip at the bottom of the bracket, just out of sight in this picture.
Last edited by a moderator: