PhilJet09
Nondescript FJR Hierarchy Displayed
Since I don't think I'll ever get one of the really nice ones made by Just Roy (anybody know if he's okay?) I decided to make my own.
I ride my bike every day, so I purchased a spare castellated nut (90179-30691-00) to use as a pattern so I didn't have to have my bike torn apart to do this. I took the nut to the hardware store and it matched up to a 1 1/4" twelve-point socket very well. The end of the socket is beveled in, so I ground it down smooth first.
Then I used the nut to mark where to make the cuts.
...and used my trusty grinder to remove the bulk of the material.
This is what I ended up with.
The length and width of the "fingers" are right, but they are still too thick to fit the nut, so I had to grind the inside edge out using my Dremel.
It isn't as pretty as Roy's, but it'll do the job and was cheap.
A little extra fine tuning with the Dremel and this is what I have.
I ride my bike every day, so I purchased a spare castellated nut (90179-30691-00) to use as a pattern so I didn't have to have my bike torn apart to do this. I took the nut to the hardware store and it matched up to a 1 1/4" twelve-point socket very well. The end of the socket is beveled in, so I ground it down smooth first.
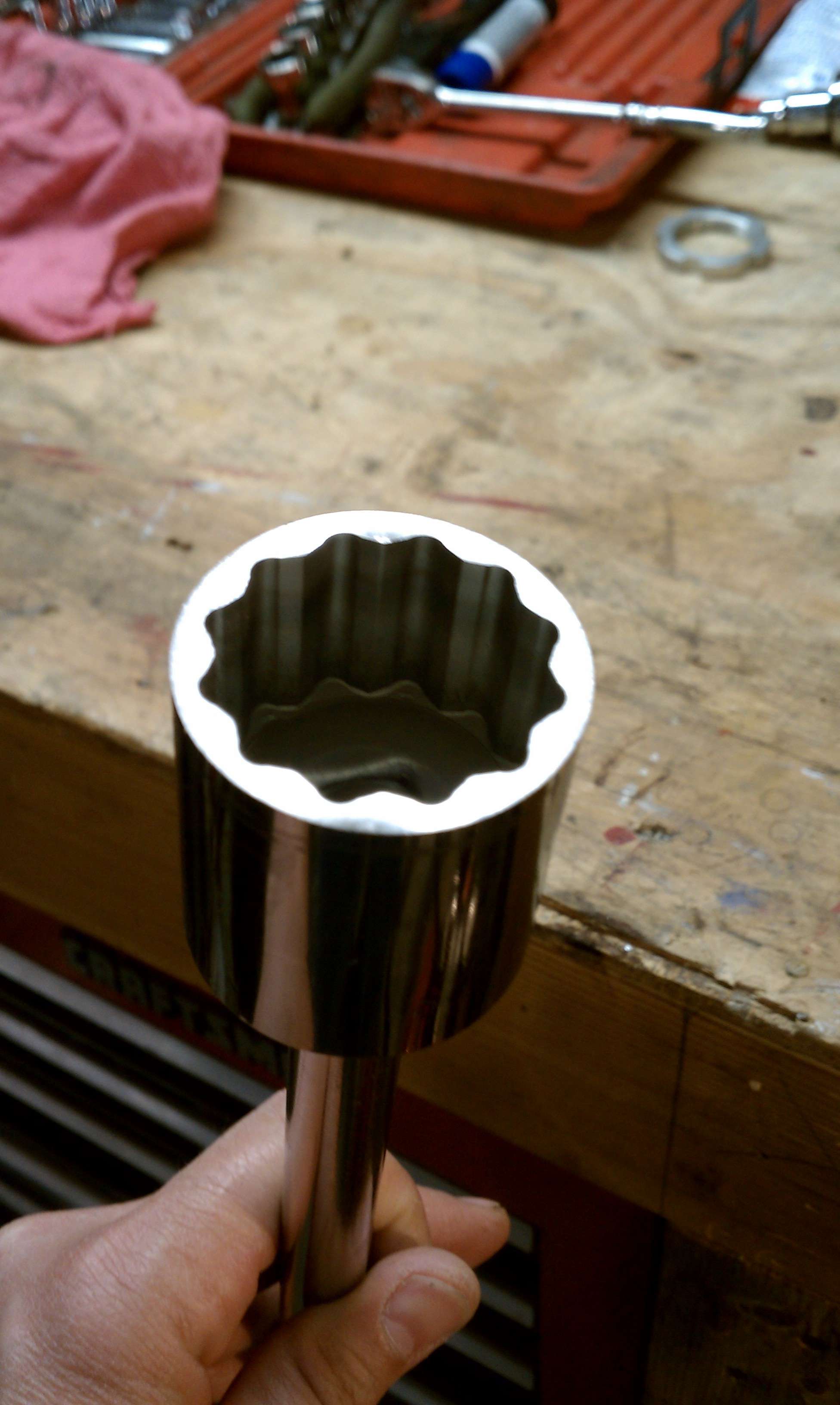
Then I used the nut to mark where to make the cuts.
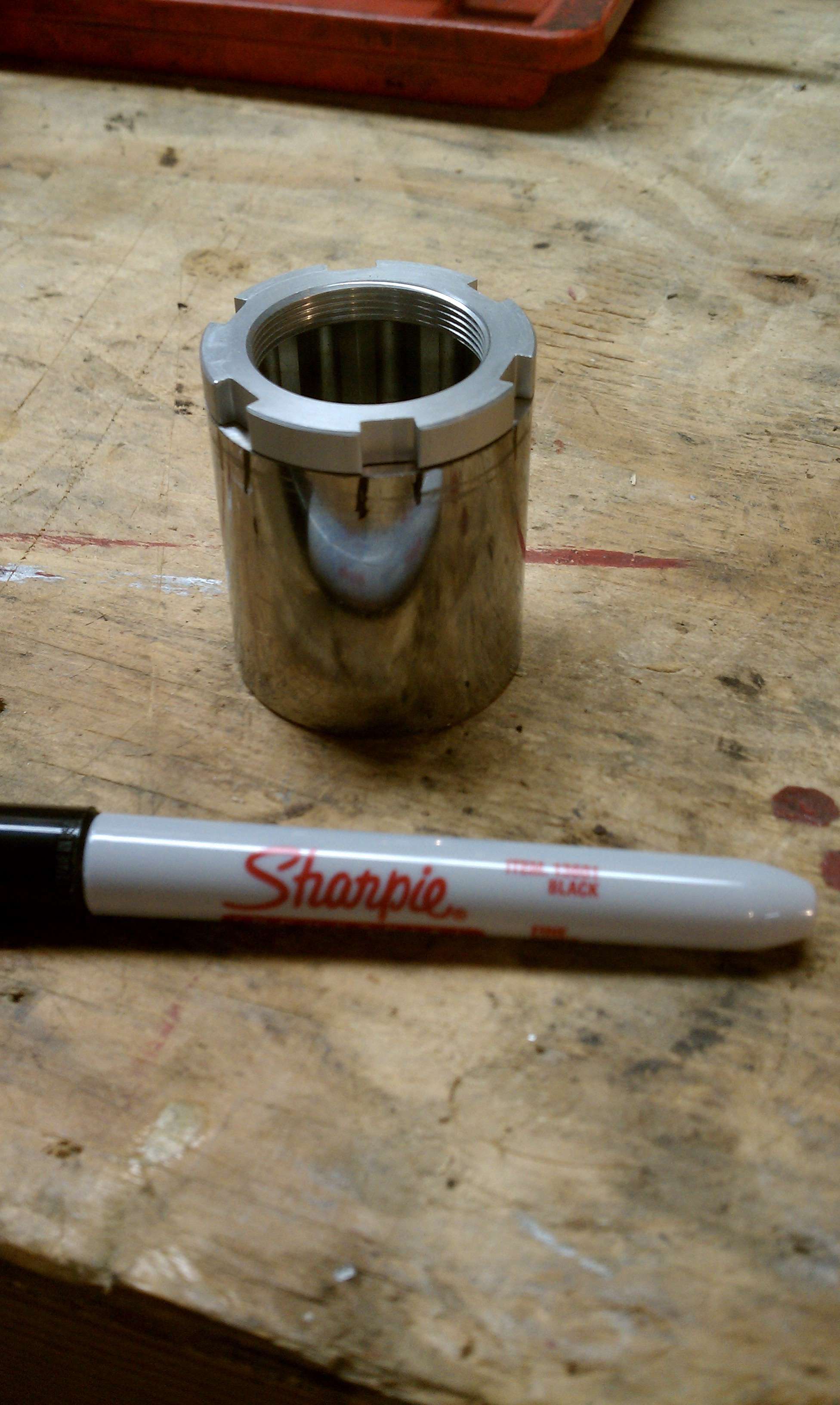
...and used my trusty grinder to remove the bulk of the material.
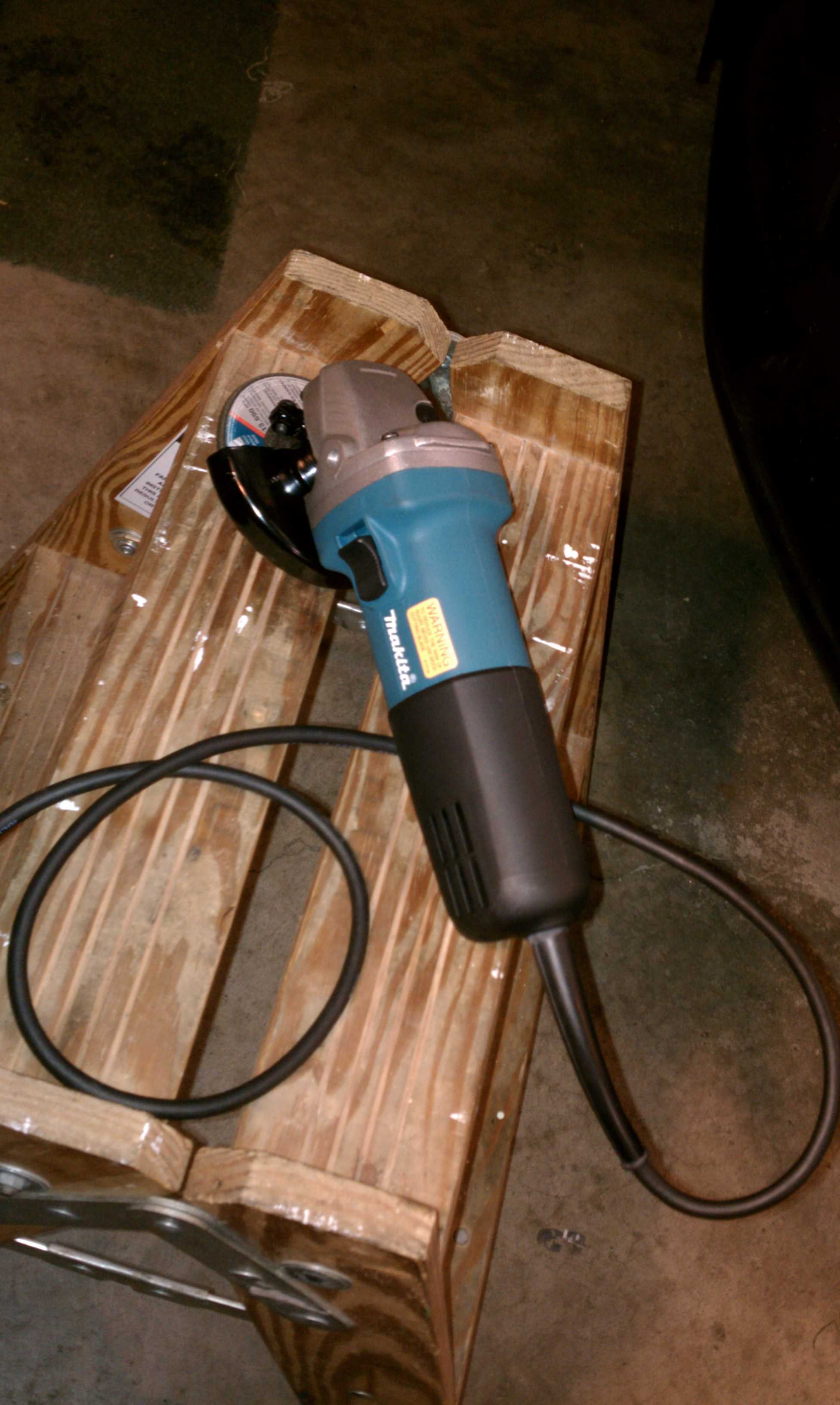
This is what I ended up with.
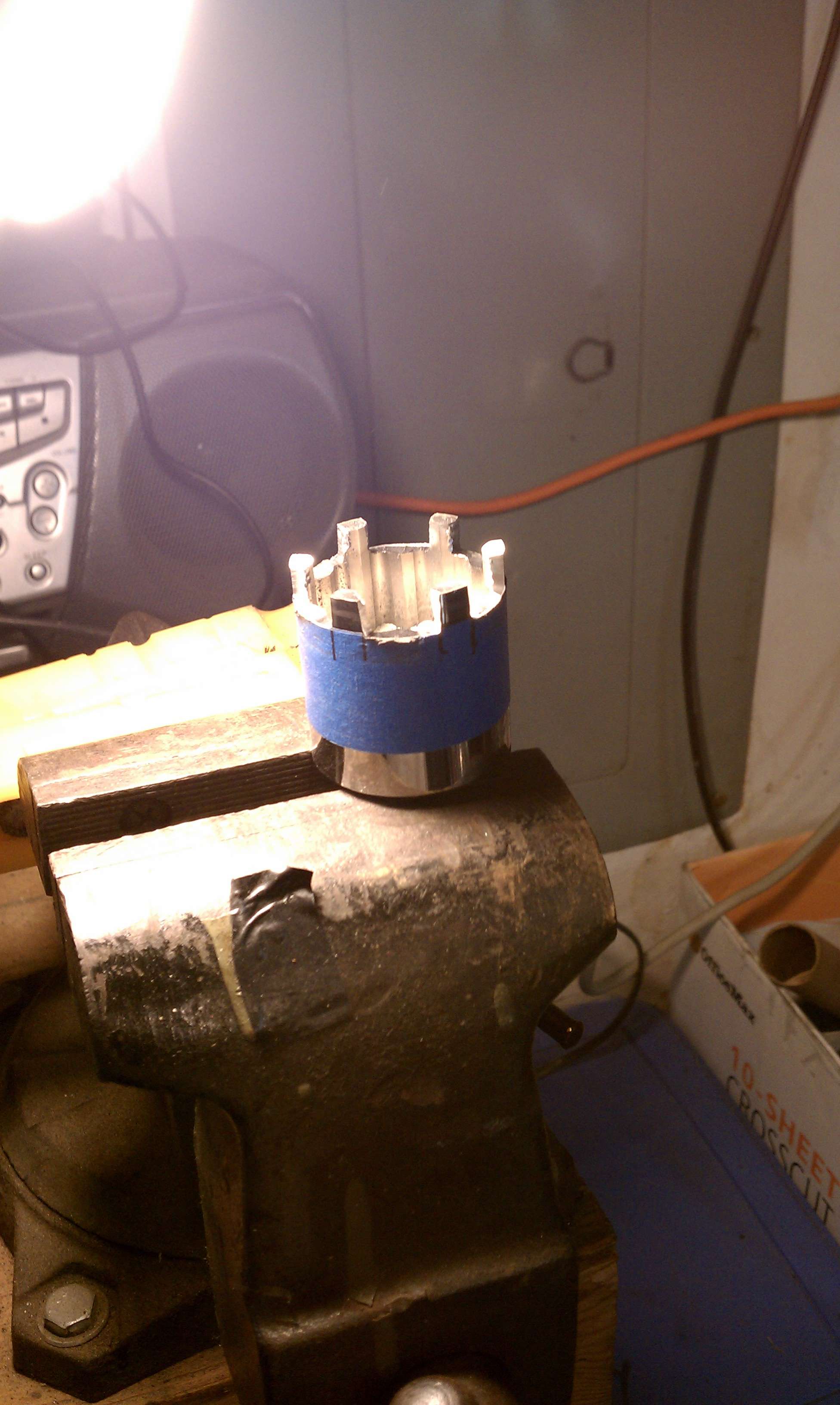
The length and width of the "fingers" are right, but they are still too thick to fit the nut, so I had to grind the inside edge out using my Dremel.
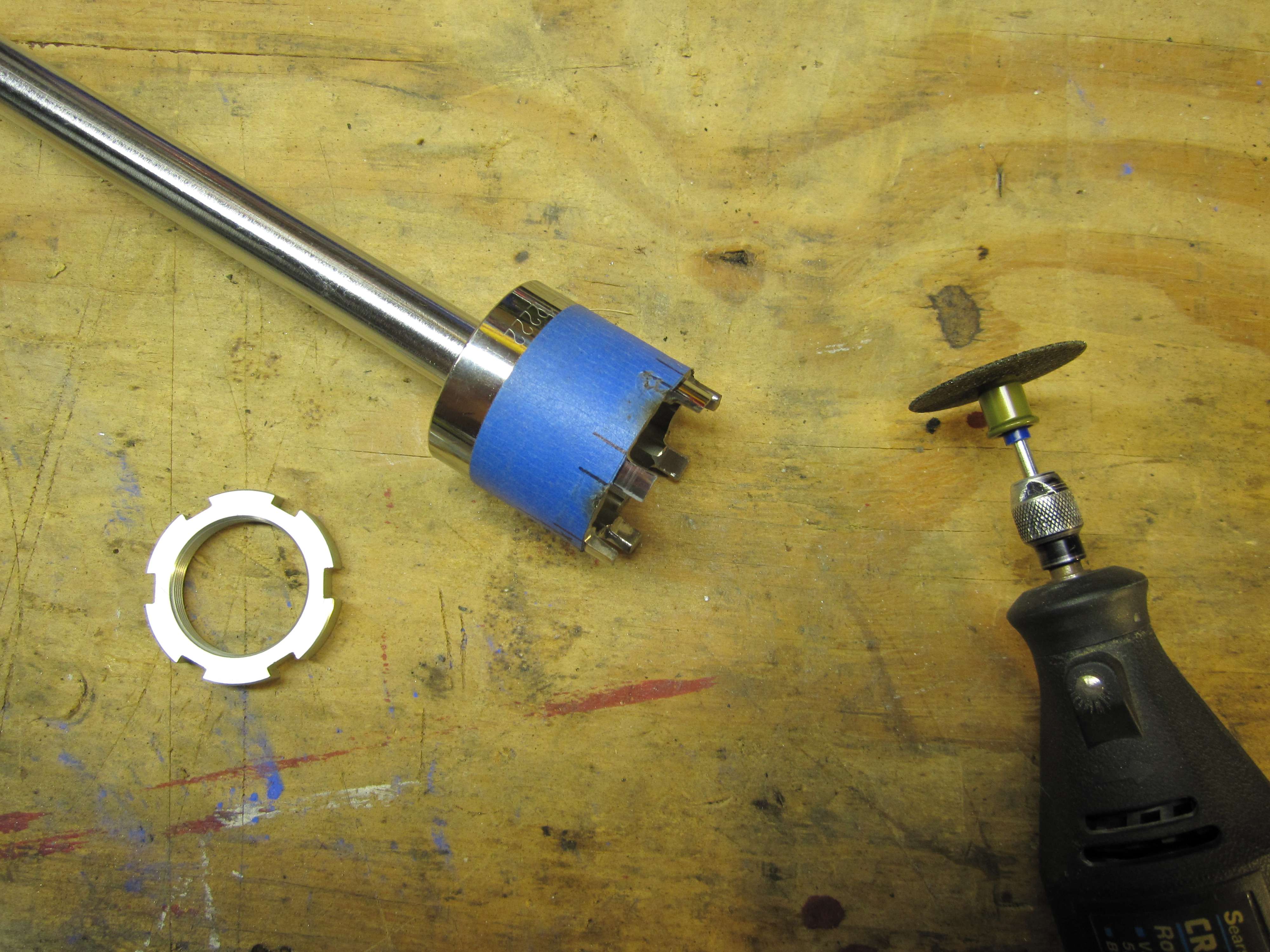
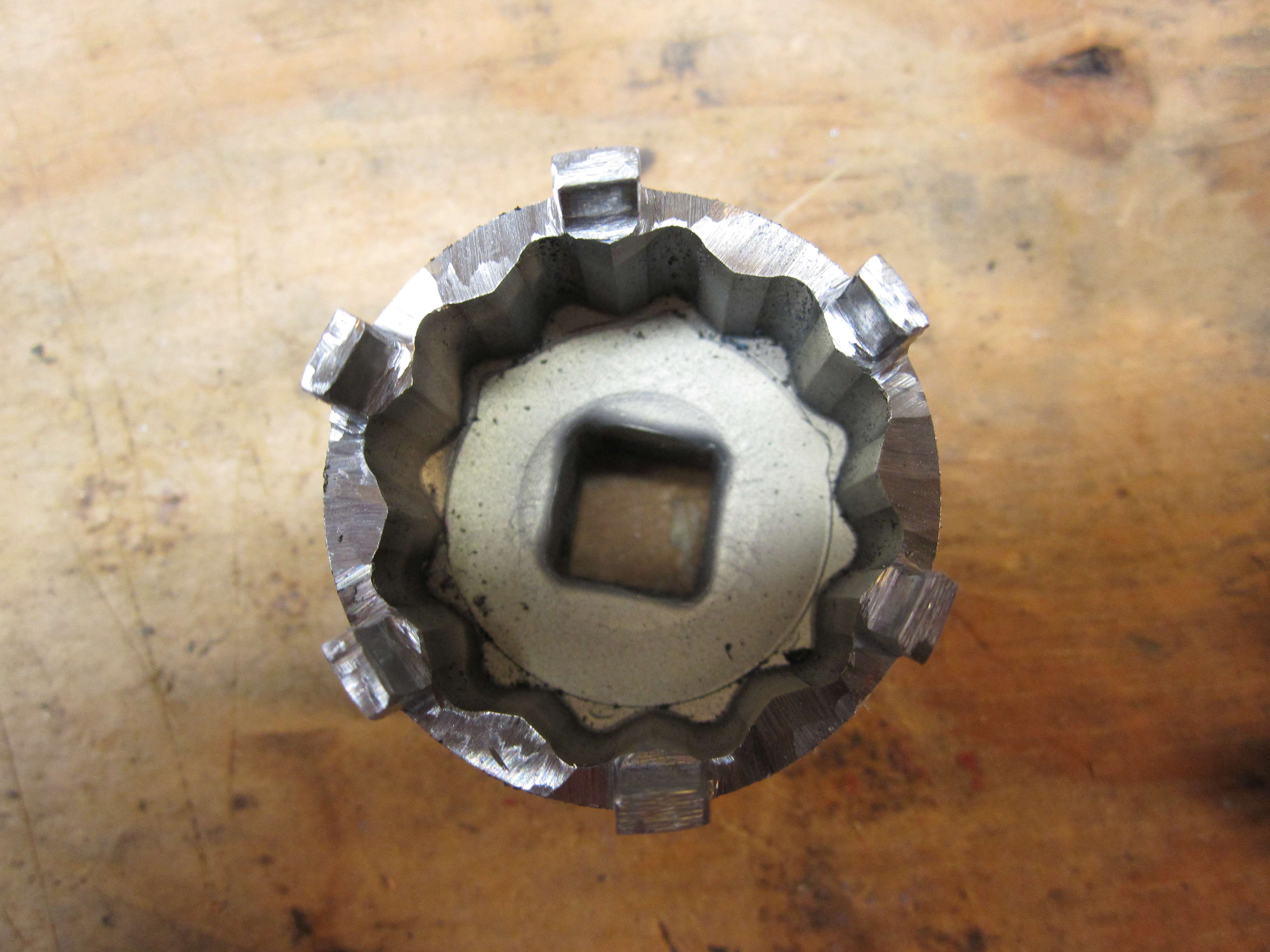
It isn't as pretty as Roy's, but it'll do the job and was cheap.
A little extra fine tuning with the Dremel and this is what I have.
