Everything you've heard on how well tuning blocks work for your windscreen is correct! Do it! It's awesome.
I've heard and read all about tuning blocks etc, on the forum. Never really seen how they work or where they went by showing it in pix. I was at Johnny80's tech day last month, and I looked at his tuning blocks on his Gen2 and thought I'm not sure my mechanism is the same, or the blocks go in the same spot on the windscreen rail. Well they do. Never having the rail off the windscreen mechanism, I didn't know, but it's similar, just shaped different.
The tuning block or spacer really (skyway calls them tuning blocks), goes between the bracket of the windscreen, Stay2 (the parts with the windscreen nuts in them), and the actuating arm (Stay leg Shield) in the middle. I got some rough dimensions and advice from Johnny80's. His V-Stream windscreen with 1/2 inch spacers hit the fairing cowling when riding due to buffeting. He had a 1/4 inch gap when standing still, but when riding it would hit or rub occasionally and eventually wore some paint down.
I originally used some washers stacked about .307 inches high, and it worked great! I then had two sets of spacers made, one set 3/8 inch the other set 1/2 inch. I tried the 1/2 inch worked OK. Got tons of air and no buffeting, no windscreen rubbing, but the arm mechanism hit my cowling and moved my cowling and dash down, a lot, almost 1/16 inch. I took it off and put on the 3/8 inch spacers. Works perfect! No interference although very close see pix. Works awesome, great air with no buffeting.
Here's where the spacers go. These are the 3/8 inch (gold) spacers installed.
This shows how close it was. I couldn't get a great pic, but it's really bloody close.
Here's the 1/2 inch spacers and screws I bought (steel and stainless steel, why not). The stock bolt on the far right is 16mm, I also purchased (right to left) 25mm, 30mm(not shown, they're installed), and 35mm. The 30mm bolts you see in the other pix don't come close to hitting the cowling but does stick out a couple threads farther then stock.
I've heard and read all about tuning blocks etc, on the forum. Never really seen how they work or where they went by showing it in pix. I was at Johnny80's tech day last month, and I looked at his tuning blocks on his Gen2 and thought I'm not sure my mechanism is the same, or the blocks go in the same spot on the windscreen rail. Well they do. Never having the rail off the windscreen mechanism, I didn't know, but it's similar, just shaped different.
The tuning block or spacer really (skyway calls them tuning blocks), goes between the bracket of the windscreen, Stay2 (the parts with the windscreen nuts in them), and the actuating arm (Stay leg Shield) in the middle. I got some rough dimensions and advice from Johnny80's. His V-Stream windscreen with 1/2 inch spacers hit the fairing cowling when riding due to buffeting. He had a 1/4 inch gap when standing still, but when riding it would hit or rub occasionally and eventually wore some paint down.
I originally used some washers stacked about .307 inches high, and it worked great! I then had two sets of spacers made, one set 3/8 inch the other set 1/2 inch. I tried the 1/2 inch worked OK. Got tons of air and no buffeting, no windscreen rubbing, but the arm mechanism hit my cowling and moved my cowling and dash down, a lot, almost 1/16 inch. I took it off and put on the 3/8 inch spacers. Works perfect! No interference although very close see pix. Works awesome, great air with no buffeting.
Here's where the spacers go. These are the 3/8 inch (gold) spacers installed.
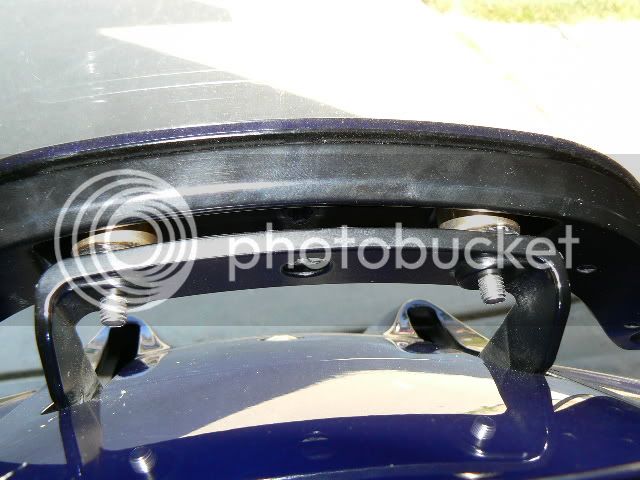
This shows how close it was. I couldn't get a great pic, but it's really bloody close.
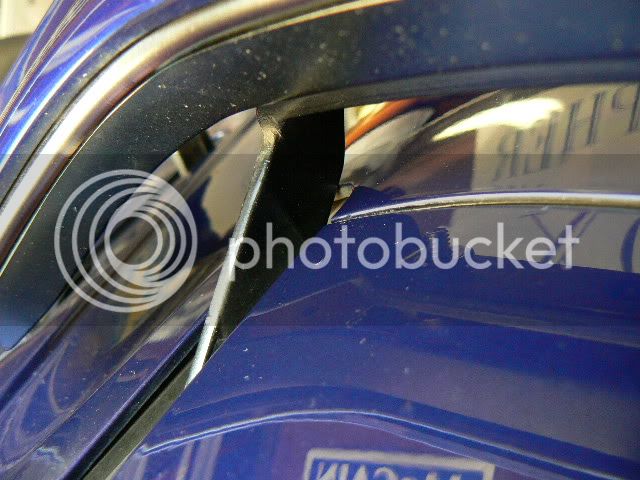
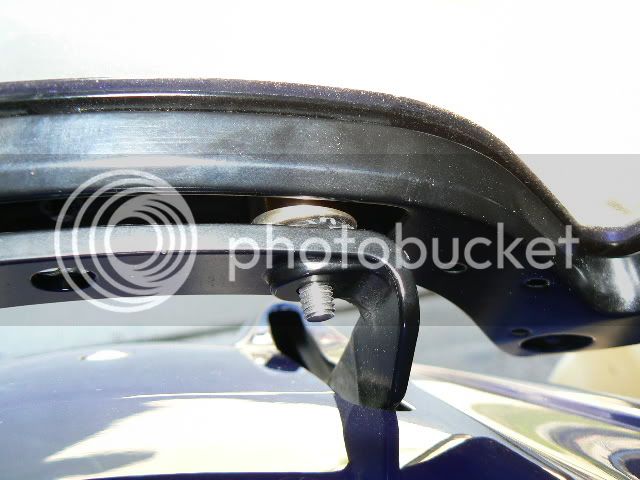
Here's the 1/2 inch spacers and screws I bought (steel and stainless steel, why not). The stock bolt on the far right is 16mm, I also purchased (right to left) 25mm, 30mm(not shown, they're installed), and 35mm. The 30mm bolts you see in the other pix don't come close to hitting the cowling but does stick out a couple threads farther then stock.
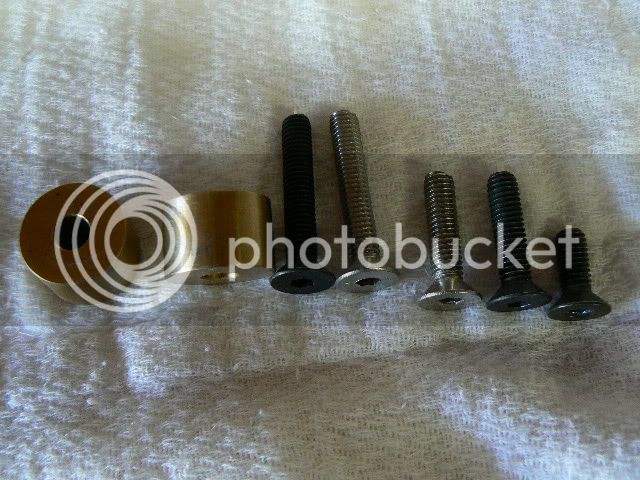
Last edited by a moderator: