I was performing the now annual relay arm service on my bike last week and noticed that the bearing sleeve in the relay arm that the dog bones attach to were showing some wear from the needle bearings:
Now just last year I replaced the other two bearings at the fore and aft ends of the relay arm along with the inner sleeves. I checked this middle sleeve and it was OK. I greased it and reassembled it. Also the other one (in the swing arm) looked fine. I'll be replacing this sleeve and the two needle bearings.
Question for any one who has replaced the middle two needle bearings: How tough is it to get them out? The end bearings are easy since you can just push them through the relay arm. It looks like the middle ones have to come out toward the nearest side. Can I just push them through from the far side like a wheel bearing? Advice appreciated. My concern is not damaging the bearing, but the relay arm. Thanks in advance.
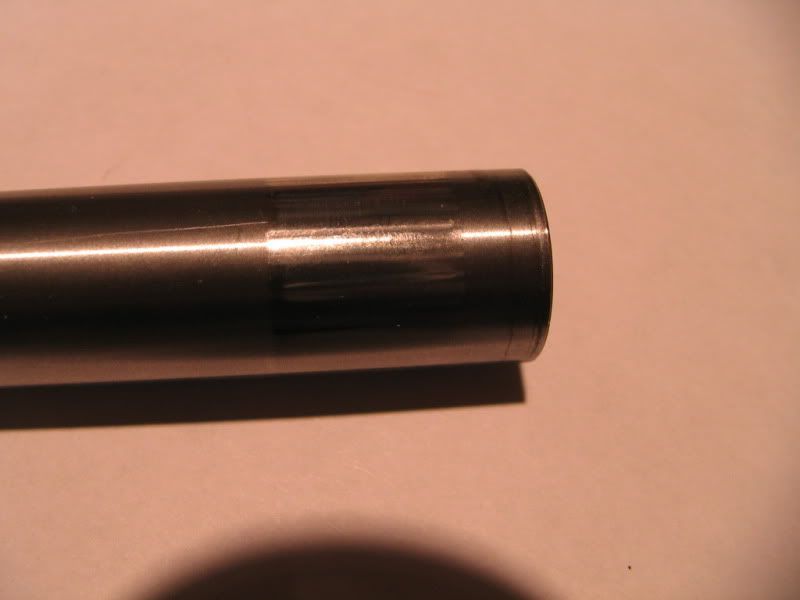
Now just last year I replaced the other two bearings at the fore and aft ends of the relay arm along with the inner sleeves. I checked this middle sleeve and it was OK. I greased it and reassembled it. Also the other one (in the swing arm) looked fine. I'll be replacing this sleeve and the two needle bearings.
Question for any one who has replaced the middle two needle bearings: How tough is it to get them out? The end bearings are easy since you can just push them through the relay arm. It looks like the middle ones have to come out toward the nearest side. Can I just push them through from the far side like a wheel bearing? Advice appreciated. My concern is not damaging the bearing, but the relay arm. Thanks in advance.