garyahouse
newbs need the forum
What an experience this was. Not one time in all the threads I've read - concerning the disassembly of these forks - did anybody mention difficulty with the washer I had to deal with today. I got one of the forks apart successfully, but it was a good thing that the air gun was able to take the allen-headed cap bolt out of the bottom of the fork - easy enough... without using my special tool. I couldn't use the special tool I had made, as the washer that sits under the spring... and just on top of the damper rod assembly - was "stuck" to - and therefore covered up... the 26mm nut on top of the damper rod assy. It kinda looks like it's designed to do so, it's a pretty snug fit, and takes a little tapping to break the washer loose from the damper assy. EDIT: Here's a pic of what I'm talking about:
So, my special tool just sat on the bench while I disassembled the fork. Once I had it apart, I could see how that washer (on which the spring sits) is designed to fit tightly on to a flange machined into the top surface of the damper rod assembly, just above the 26mm nut. Mine kinda welded itself on there. By rocking it it back and forth with a soft mallet, sorta teeter-totter style, it popped off eventually, but that was after I removed the damper rod assy. With the washer removed, now the 26mm "nut" cast into the top of the damper rod assy is visible and accessible. Heading back out to work on it some more. Took lotsa pictures... will post later.
HPPANTS
The spacer you spoke of above: Is that the washer that fits over the 26mm "nut" on the top end of the damper assy... just under the spring - that I spoke about above?
Also:
Ran into a jam. Can't drive the top bushing in (it goes under the seal). The 2" dia schedule 40 PVC simply slides over the top of it, and the bushing wedges inside the pvc... rather than driving down into the a machined pocket where it belongs. It's a smaller diameter than the oil seal that would go in afterwards. Looks like the PVC ain't gonna work for the bushing. UGGH.
EDIT:
Just read this post (CLICKY) by FJRed back in 2011. He used a Chrome exhaust tip from Advance Auto Parts - that he cut down... to drive the seals in. They still sell the same item (but it costs a little more... figures). So I bought one. Now I just gotta figure out how to cut it down nice and square and straight. This oughta be interesting???
Gary
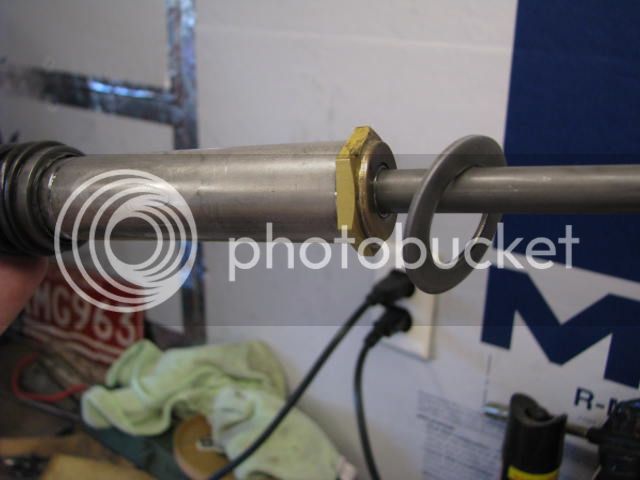
So, my special tool just sat on the bench while I disassembled the fork. Once I had it apart, I could see how that washer (on which the spring sits) is designed to fit tightly on to a flange machined into the top surface of the damper rod assembly, just above the 26mm nut. Mine kinda welded itself on there. By rocking it it back and forth with a soft mallet, sorta teeter-totter style, it popped off eventually, but that was after I removed the damper rod assy. With the washer removed, now the 26mm "nut" cast into the top of the damper rod assy is visible and accessible. Heading back out to work on it some more. Took lotsa pictures... will post later.
HPPANTS
The spacer you spoke of above: Is that the washer that fits over the 26mm "nut" on the top end of the damper assy... just under the spring - that I spoke about above?
Also:
Ran into a jam. Can't drive the top bushing in (it goes under the seal). The 2" dia schedule 40 PVC simply slides over the top of it, and the bushing wedges inside the pvc... rather than driving down into the a machined pocket where it belongs. It's a smaller diameter than the oil seal that would go in afterwards. Looks like the PVC ain't gonna work for the bushing. UGGH.
EDIT:
Just read this post (CLICKY) by FJRed back in 2011. He used a Chrome exhaust tip from Advance Auto Parts - that he cut down... to drive the seals in. They still sell the same item (but it costs a little more... figures). So I bought one. Now I just gotta figure out how to cut it down nice and square and straight. This oughta be interesting???
Gary
Last edited by a moderator: